Из концепта — в серию
10 сентября 2020
Как проектируют тормозные колодки?
Меня все время поражало, насколько извилистый путь проходит автомобиль с момента дизайнерского эскиза до серийного производства, где все этапы этой сложной цепи — изготовление концепт-кара, маркетинговые исследования, разработка технологических карт, создание ходовых образцов, тестовые испытания и т. д. — тесно взаимосвязаны друг с другом. И ведь параллельно с созданием каждого нового средства транспорта схожий эволюционный путь проходят составляющие этого конечного продукта — автокомпоненты. В этот раз затронем тормозную систему: Денис Двали, технический специалист ООО «ТМД Фрикшн Евразия», расскажет нам о наиболее значимых этапах проектирования тормозных колодок для OEM.
Беседовал Иван СОКОЛОВ
Любой автомобиль разрабатывается группой представителей инженеров автоконцерна совместно с компаниями — разработчиками отдельных его узлов. Тормозная система является сложной и многокомпонентной системой, начиная от педали тормоза и заканчивая исполнительными тормозными механизмами на каждом из колес. И разработчик тормозов на основе данных технического задания от автопроизводителя (скоростные, мощностные, габаритные и весовые параметры автомобиля, а также требования к тормозному пути) разрабатывает соответствующих размеров и характеристик конструкцию тормозных механизмов.
Textar, как разработчик рабочей тормозной системы (под этим определением я подразумеваю непосредственно тормозные механизмы каждого из колес — тормозные диски/барабаны и колодки), занимается только своим направлением, при этом другие элементы тормозов — гидросистема, блоки ABS, усилители тормозов — являются прерогативой других узкоспециализированных производителей. Стоит отметить, что в последние годы в ассортименте бренда появились технические жидкости (смазка, очистители тормозов, тормозная жидкость), специнструмент для обслуживания тормозов, а также датчики ABS, но эти компоненты поставляются на вторичный рынок запчастей.
1. Форма и содержание. Определяем дизайн колодок
Детали тормозной системы — тормозной диск, колодки, суппорт — разрабатываются производителем автокомпонентов на основании имеющихся опыта, прототипов, наработок и расчетов. Если по каким-то причинам у разработчика нет возможности применить уже имеющиеся наработки, то механизм проектируют с нуля. Вариантов развития коммуникации и между автопроизводителем и производителем компонентов в основном два.
В первом случае автопроизводитель на основании собственных представлений, разработок и чертежей дает разработчику техническое задание, которое предусматривает создание фрикционного материала и его конструкции. При этом форма самой колодки может быть в той или иной степени определена автопроизводителем заранее, и разработчик тормозов может менять ее лишь в определенных узких рамках.
Второй путь создания автокомпонента — когда автопроизводитель и производитель тормозных колодок начинают совместную разработку элемента с нуля, определяя будущий дизайн и характеристики элемента общими усилиями.
Как бы то ни было, но либо в результате анализа ТЗ по конфигурации изделия, либо после совместных работ мы приходим к пониманию дизайна колодки с заданными параметрами.
2. Расчет коэффициента трения
Следующий этап при создании тормозного компонента — разработка фрикционной смеси. Дело в том, что в самом начале работы над продуктом у разработчика тормозов нет конкретики по конечным характеристикам колодки. В основном у него есть лишь ориентировочные представления о взаимосвязях между формой колодок, составом их фрикционной смеси и характеристиками будущего автомобиля. При этом разработчик тормозных дисков у автомобиля может быть один (и он отвечает за эту конструкцию), а разработчик колодок — другой. Это, впрочем, не мешает им между собой коммуницировать на этапах создания своих продуктов.
Конечная цель — создание определенного тормозного момента на каждом из колес, который, в свою очередь, зависит от силы трения и диаметра тормозного диска. Допустим, конструкторы автопроизводителя знают, как будет тормозить авто и какими средствами для достижения этой цели они располагают (масса и размеры автомобиля, давление в гидросистеме, размеры тормозных дисков, поршней, суппортов и т. д.). Имея эти данные, разработчик тормозов должен просчитать коэффициент трения будущих колодок.
Рассчитывается этот параметр из известной формулы: Fтр = μ N, где Fтр — сила трения, N — сила нажатия, или сила, с которой колодка прижимается к диску, μ — коэффициент трения. Сила нажатия зависит от тормозной системы в целом (от конструкции педали тормоза, от конструкции суппорта, от соотношения диаметров поршней главного и рабочего тормозных цилиндров, от вакуумного усилителя и т. д.) и известна заранее. Зная также силу трения, можно определить коэффициент трения μ, который и задается разработчику смеси.
3. Разработка фрикционного материала
Проблема в том, что коэффициент трения, который мы задали разработчикам, плавающий — он сильно изменчив и может меняться в зависимости от температуры, скорости, давления, с которым колодка прижимается к диску. Есть и другие параметры, влияющие на трение, — влажность воздуха, наличие реагентов на дороге, степень износа тормозных элементов — они менее существенны, но все же также влияют на эффективность торможения. И тут начинается то самое таинство — процесс создания колодки, когда нужно собрать из базовых элементов фрикционный материал, который обеспечит коэффициент трения в заданном диапазоне во всех возможных вариантах эксплуатации автомобиля.
Но коэффициент трения, как выясняется, это только полдела. Колодка при этом должна охлаждаться, иметь определенную теплопроводность (это также достигается составом, в том числе за счет внедрения в него разных металлов), обеспечивать такие параметры, как стойкость к истиранию (клиенты не любят часто менять колодки), а также по возможности не изнашивать быстро тормозной диск. Последнее учесть, к слову, удается не всегда, так как особенно «цепкие» и, следовательно, эффективные фрикционные составы не очень-то берегут тормозной диск.
Параметры, которые влияют на состав фрикционной смеси:
- стоимость тормозных колодок
- шумовые характеристики
- жесткость фрикционного слоя
- пыльность и экологичность
- тип фрикционной смеси
4. Поиски баланса. Учет параметров ТЗ производителя
Итак, каким образом все эти параметры влияют на конечный результат? Начнем с жесткости колодки (этот параметр обозначается в прямом смысле, то есть жесткость самой колодки, а не жесткость торможения). Например, проще сделать колодку хорошо тормозящую и не скрипящую, но при этом мягкую, что напрямую отобразиться на таком параметре, как «чувство педали». Это, вроде бы, обиходное выражение имеет вполне техническое основание: человек при нажатии на педаль должен отчетливо понимать, каким образом нажатие на педаль влияет на замедление автомобиля. При этом это чувство педали должно быть стабильным и прогнозируемым. Если была применена мягкая колодка, то водитель теряет чувство стабильности, что негативно сказывается на безопасности, и процесс торможения после нажатия на педаль, к примеру, может происходить нелинейно, скачками.
Пыльность и экологичность. Эти параметры автопроизводитель может выдвигать в числе наиболее важных, так как это является сегодня неким трендом. Например, в США прижились полуметаллические колодки (Semi-Metal), которые выбирались местными автопроизводителями из-за их надежности, низкой цены и малопыльности: американские автовладельцы предпочитают ездить на красивых машинах с блестящими и чистыми колесными дисками.
К слову, с типом фрикционной смеси производитель тормозных механизмов может определиться еще на ранних этапах разработки. Бывают колодки с низким содержанием стали (Low Steel), полуметаллические колодки (Semi-Metal), а также колодки из безасбестовой органики (NAO, Non-Asbestos Organic). Если у автопроизводителя в приоритете эффективность торможения авто, то выбор падет, скорее всего, на колодки Low Steel. То есть сначала выбирается тип материала, а уже после просчитывается баланс тех или иных компонентов для получения нужного результата. Так, рецепт смеси либо выбирается из уже имеющихся формул (поскольку у Textar внушительный опыт разработки, то и библиотека формул собралась весьма приличная), либо, если по каким-то причинам ничего не подходит, разрабатывается новый рецепт смеси.
Понятно, что при таких процессах важную роль играет себестоимость материалов, поэтому приблизительная стоимость конечного продукта согласовывается с автопроизводителем.
5. Создание прототипа
Следующий этап — создание колодки-прототипа. Материалы собираются поштучно, прессуются в специальных формах на опытном производстве, после чего начинаются стендовые испытания. В первую очередь, конечно, проверяется эффективность торможения, далее — шумы, пыль, износ и т. д. Если что-то не получается, смесь начинают дорабатывать. Если все нормально, то изготавливается пилотная полупромышленная партия колодок — используется в этот раз уже стандартное производственное оборудование. Это делается для того, чтобы, во-первых, на стендах протестировать колодки, изготовленные промышленным способом, а во-вторых, чтобы установить такие колодки на тестовые автомобили и протестировать их в реальных условиях.
6. Этапы тестирования
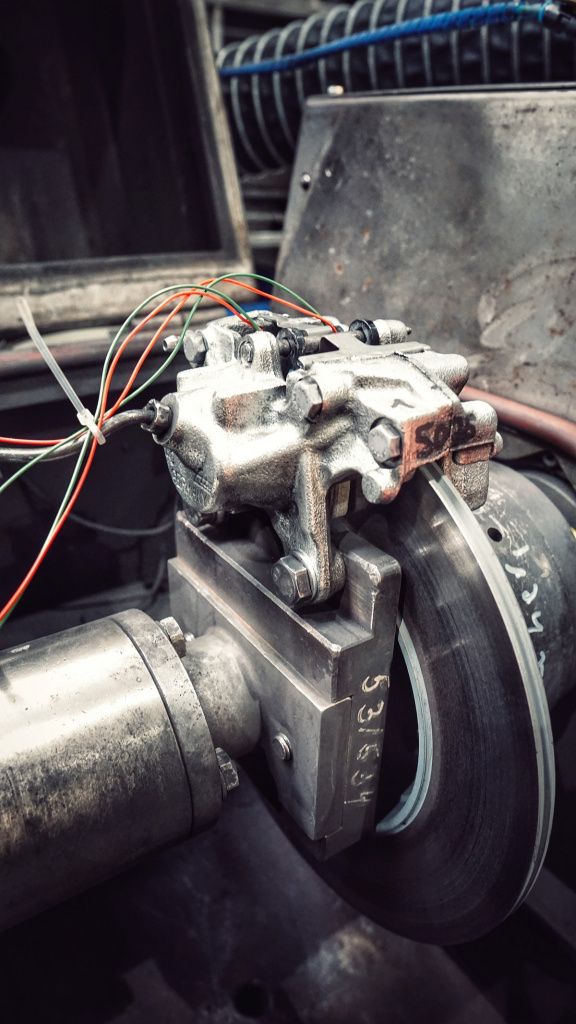
Первоначальные испытания включают в себя ряд стандартизированных тестов. И если на самых ранних этапах колодки тестируются в специальных лабораториях, где применяется универсальная оснастка, то в процессе эволюции от опытного к серийному образцу колодка тестируется в составе всей тормозной системы автомобиля уже на реальных автомобилях — как в рамках тестового полигона, так и на дорогах общего пользования.
Так, один из наиболее известных тестов — испытание, разработанное авторитетным немецким журналом «Auto Motor und Sport» (AMS), которое с течением времени стало неким стандартом в отрасли. Его используют многие ведущие производители колодок в том числе для того, чтобы сравнивать компоненты между собой. Тест представляет собой последовательную серию из десяти торможений со скорости 100 км/ч до нуля. При этом замеряется длина тормозного пути при первом торможении на «холодных» колодках и при последнем, когда колодки уже раскалены. Испытательный автомобиль с сидящими в нем водителем и пассажиром загружается до максимально разрешенного веса. Другое, более жесткое испытание — тест HFT (High Friction Temperature), определяющий стабильность характеристик колодок при многократных торможениях с 90 % от максимальной скорости до полной остановки.
Тестирование на дорогах общего пользования более жизненное: испытатели оценивают комфорт при торможении, степень износа колодок, эффективность торможения, наличие скрипов. В общем, это те ситуации, с которыми водители сталкиваются постоянно. Так, одна модель колодок на испытаниях проходит минимум 300 тыс. км (для ускорения запуска колодок в серию испытания компонентов одновременно проводятся в разных странах и в разных условиях).
Если речь идет о колодках, которые пойдут на конвейер в качестве оригинальных комплектующих, то после окончательных тестов они проходят испытания на соответствие европейским стандартам, но уже в составе готовящегося к выпуску автомобиля (у каждой страны — свои испытания и требования).
Но если линейка колодок будет поставляться на aftermarket, то согласно европейским правилам ее нужно испытать по стандартизированной программе ECE-R90, которая частично схожа с заводскими испытаниями. Основная задача этих тестов — доказать, что в определенных диапазонах автокомпонент соответствует оригинальной колодке по своим показателям. Например, по эффективности торможения колодка не должна отличаться более чем на 15 % в ту или иную сторону, фрикционный материал должен прочно держаться за основание колодки, а сжимаемость колодки не должна превышать 5 % от ее толщины при 400 °C. И даже если колодка та же самая, что идет в качестве оригинальной комплектующей и не отличается от нее по качеству, она все равно должна пройти эти испытания. Именно поэтому запуск в производство нового компонента — это столь длительный процесс: от начала разработки линейки тормозных колодок до ее поставок на автоконвейер в среднем проходит 2–3 года (на aftermarket, соответственно, колодки поступают быстрее).
7. Работа с отзывными компаниями и гарантийные обязательства
Что касается послепродажного обслуживания, то изредка бывают случаи, когда в реальной эксплуатации колодки ведут себя несколько иначе, чем на тестовых испытаниях, — например, если колодка показала неудовлетворительные шумовые характеристики. И если в этом случае превышен определенный уровень рекламаций, то производитель приступает к модернизации данной линейки колодок: изменяется либо состав фрикционной смеси, либо общий дизайн колодки. Один из стандартных способов коррекции теплопроводности колодки или борьбы со скрипами — добавление промежуточного слоя между основанием колодки и фрикционным составом. Такое вмешательство в конструкцию может происходить как при отзывной кампании, так и являться «улучшением на ходу», когда производитель модернизирует автокомпонент после выпуска его в серию.
Отзывные кампании проводятся по двум причинам: либо из-за конструктивных недоработок в продукте, либо из-за производственного брака. Для потребителя это выглядит одинаково, но производителю важно найти причину брака. В таких случаях производство останавливается до того времени, когда проблема будет решена. Все вышеперечисленные процессы — разработка дизайна колодки и ее фрикционной смеси, лабораторные и ходовые испытания, прохождение тестов на соответствие нормам международных стандартов, а также гарантийные обязательства — в конечном итоге влияют как на качество продукции, так и на ее конечную себестоимость. Эти факторы необходимо учитывать при подборе автокомпонентов для ремонта и техобслуживания автомобиля.
Еще никто не оставил свои комментарии. Ваш комментарий будет первым.