«Лужу, паяю, раритет починяю…»
6 августа 2015, Евгений Магаков
Помните, раньше в журналах была такая рубрика: «Вы нам писали!»
Попробуем наладить обратную связь с читателями, приславшими письма с вопросами о лужении кузова в процессе ремонта, и попробуем рассекретить технологию с комментариями фото техпроцесса.
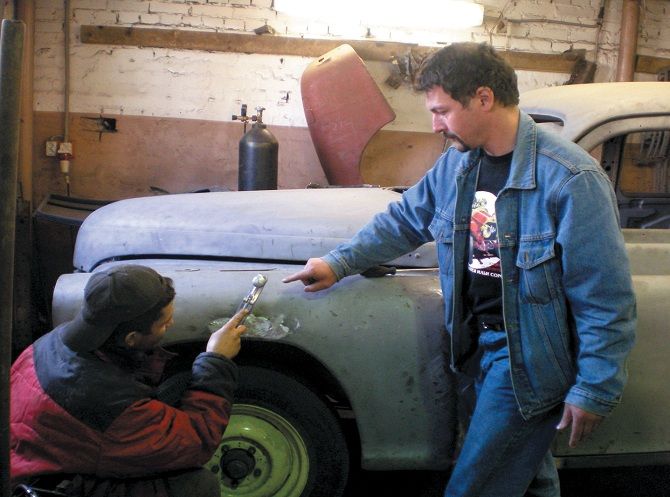
Немного истории
На заре массового автомобилестроения штампы кузовного производства на автозаводах были несовершенны, частая смена матриц и пуансонов не способствовала 100%-ной повторяемости деталей, а значит, на нитке конвейера рабочим приходилось заниматься их доводкой и подгонкой по месту. Кроме того, все сварные швы и технологические стыки на внешних поверхностях надо было как-то скрыть, при этом прочно и незаметно. Многие детали перед установкой на кузов приходилось сваривать из нескольких элементов воедино, так как не было возможности изготовить их из цельного листа металла просто штамповкой. Так, передние крылья «Победы» состояли из двух частей, сваренный контактной сваркой шов надо было защитить и сделать невидимым с внешней стороны. На фотографиях отпескоструенного (рис. 1, 2) кузова хорошо видна поверхность металла, покрытая припоем, именно он позволял наносить достаточно толстый выравнивающий слой при хорошей адгезии к основе и прочности на изгиб.
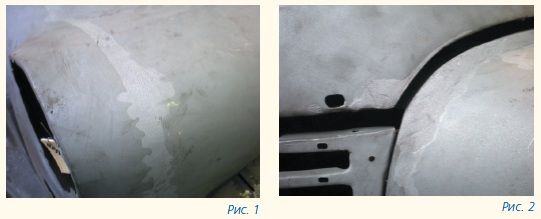
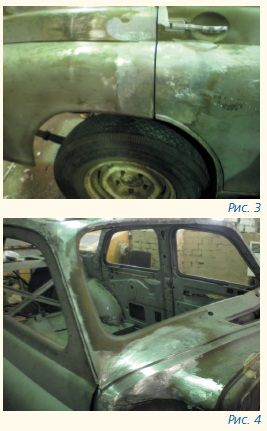
Но не будем отвлекаться от нашей темы. Почему вообще сегодня встал вопрос об опайке кузова при проведении реставрационных работ? Может, гораздо проще использовать достижения современной автохимии в этой области, ведь полиэфирные шпатлевки уже «научились» хорошо держать толщину слоя, легко обрабатываются абразивом, прекрасно окрашиваются, могут содержать в
себе разные наполнители для прочности или, наоборот, эластичности, или все не так просто? Рассмотрим кузов вооруженным глазом.
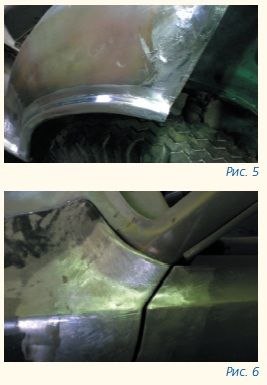
Срывая покровы
Безусловно, работать при подготовке кузова к окраске проще и быстрее полиэфирными шпатлевками: намазал, подождал, срезал все лишнее — и готово. Хоть поверхность и получается гладкой, и ей можно придать желаемую форму, но что будет потом, после полной полимеризации смолы? Представим себе плитку нагретого в кармане шоколада в фольге; сняв бумажную обертку, попробуем согнуть плитку двумя руками. Сам шоколад, будучи пластичным, согнется в дугу, а вот фольга порвется на поверхности в клочья. Почему? Да просто у каждого материала есть характеристика – коэффициент линейного расширения. И при совместном использовании двух и более материалов всегда надо
заранее просчитывать их совместимость. В угоду ускорению процесса авторемонта, учитывая относительно небольшой ресурс жизни кузова в 7–10 лет, заложенный автопроизводителями (если делать «вечный» автомобиль, никто не купит новый), технология шпатлевания — это некий компромисс между долговечностью отремонтированного участка и временем нахождения автомобиля в ремзоне.
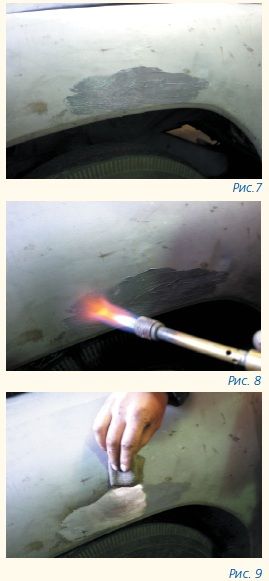
Учитывая тот факт, что кузов автомобиля не вырублен из цельного куска мрамора и подвержен знакопеременным нагрузкам (проще говоря, он гнется в разных местах по-разному), то надо и покрытия наносить с учетом возможных вибраций, деформаций и изгибов. Помните, Шерлок Холмс в исполнении Василия Ливанова в «Пестрой ленте» со словами «Ворвался, натоптал, и-И-и-и-спортил ха-а-а-арОшу-у-у-ую ве-Е-ещь» разогнул обратно каминную принадлежность? Если согнуть пруток припоя, вполне можно повторить экранный трюк Василия Ливанова, когда его герой — Шерлок Холмс — в «Пестрой ленте» со словами «Ворвался, натоптал, и-И-и-и-спортил ха-а-а-арОшу-у-у-ую ве-Е-ещь» разогнул обратно каминную принадлежность. Если попытаться произвести это с колбаской из заполимеризовавшейся шпатлевки, то лучше это делать в защитных очках: осколки разлетятся во все стороны. Либо пойти дальше и взять два металлических прутка, один покрыть добрым слоем припоя, второй зашпатлевать и повторить над ними экзекуцию. Думаю, результат вполне предсказуем, вот только кузов в отличие от толстого прутка более нежен и нуждается в защите от коррозии гораздо сильнее. Приведенный пример, конечно, гипербола, но достаточно хорошо демонстрирует плюсы использования при реставрации именно припоев, особенно на кромках и стыках, там, где риск отломить хрупкое, но твердое покрытие шпатлевки особенно велик. Разумеется, фанатично выводить все без исключения плоскости и радиусы на 100% только опайкой было бы неразумно, тратить дорогое время и припой на финишную доводку рисок и царапин неоправданная роскошь, лучше доверить эту работу химии. Вопрос именно в толщине наносимого слоя, ведь припой в 7–9 мм выдержит удар молотка рядом и непосредственно по нему, а вот его оппонент — вряд ли. Нанесенный слой доводочной шпатлевки на припое ничуть не испортит картину, ведь в тонком слое он тоже вполне эластичен. Вырисовывается следующая технология ремонта: на отпесоченный и проваренный кузов с навешенными панелями наносится флюс для опайки, по нему оловянно-свинцовый припой ПОССу 30-2, после выравнивания и зачистки наносятся защитные грунты, шпатлевки, затем грунты-поронаполнители, проявочный слой и производится финишная окраска.
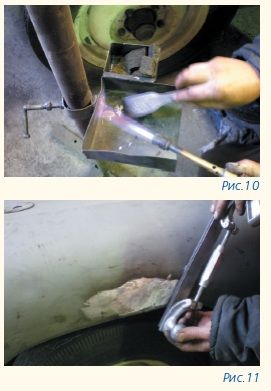
«Памеедленней, пжлста, я запппсываю!»
Пришло время более детально рассмотреть весь процесс превращения дефекта на кузове в блестяще (в буквальном и переносном смысле) отремонтированный участок. На серии фотографий можно понять область применения такой технологии (рис. 3–8) – ребра, нерихтуемые места, сварные швы, выведение зазоров и получение идеальной геометрии – все это по плечу мастеру, вооруженному горелкой и деревянным шпателем. Начнем процесс с легкого шлифования нужного участка абразивом и продувкой сжатым воздухом для удаления пыли от песка и зерен наждачной бумаги. Затем, понимая, что просто так припой к железу не прилипнет, надо подготовить поверхность – создать тончайшую оловянно-свинцовую пленку, на которую уже можно смело лепить нужный слой. Готовить будем специальной пастой фирмы WURT, все достаточно просто и не требует особых навыков (рис. 7). Нанесли кисточкой состав из банки (причем лучше не пользоваться прилагаемой к ней, а взять помягче – расход материала уменьшится за счет толщины нанесения), прогрели пропановой горелкой, стерли тряпкой, поверхность превратилась из серой матовой в блестящую, готово. Не стоит перегревать поверхность, подгорит основа полуды, останутся пятна, достаточно просто заметив легкое вскипание, переместить горелку и вытереть, не дожидаясь остывания (рис. 8–9). Далее в лоточке разогреваем пруток припоя ПОССу30-2 до размягчения и, как сливочное масло на бутерброд, наносим до отвердевания деревянной лопаточкой, пропитанной в масле (рис. 10). Нарастив необходимую толщину, прогреваем слой горелкой, еще раз разглаживаем и после остывания в течение 1–2 минут можно брать в руки рихтовочную пилу и придавать поверхности требуемую форму (рис. 11). При необходимости повторяем процесс нанесения припоя до получения нужной толщины слоя с запасом на срезание при шлифовке. Дальше можно наждачной бумагой на шлифке или вручную доводить деталь до совершенства, уменьшая риски и кратеры. А дальше вступают в дело автомаляры, и по подготовленной таким образом поверхности работают с эпоксидными грунтами, с доводочной тиксотропной шпатлевкой, грунтами-наполнителями и прочими привычными расходными материалами.
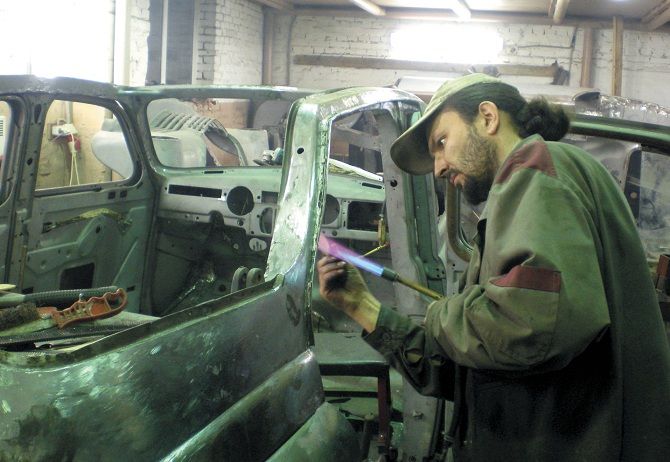
Комментарии
Рекомендованные статьи
Еще никто не оставил свои комментарии. Ваш комментарий будет первым.