Так делают свечи Bosch
30 января 2013, Марина Белоглядова
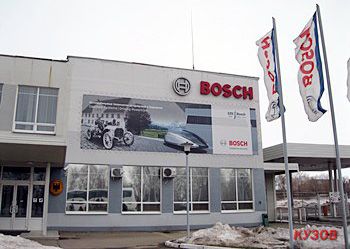
В прошлом году одним из самых интересных мероприятий, организованных компаний Bosch для представителей СМИ, был международный пресс-тур, в рамках которого состоялась экскурсия по огромному складскому комплексу, посещение завода по производству свечей зажигания в городе Бамберге и поездка на российское предприятие ОАО «Роберт Бош-Саратов» в город Энгельс.
Открывал мероприятие конференции старший вице-президент компании, после которого Кристоф Декэ представил стратегию Bosch в сегменте рынка тормозных систем: «На предприятиях компании будут выпускаться детали тормозной системы под своим брендом, а также и по заказу от других компаний для рынка послепродажного обслуживания. Производство тормозных дисков для сегмента ОЕ расположено в Бранденбурге, в компании есть лаборатория качества, ее штат состоит из десяти человек, которые занимаются ежедневно только проверкой качества тормозных дисков. В итоге можно сказать, что благодаря инженерной компетенции, собственным производственным мощностям и налаженному графику поставок, компания Bosch уверенно завоевывает данный сегмент рынка».
Дистрибьюторский центр в Карлсруэ
После официальной части состоялась экскурсия в дистрибьюторский центр компании в Карлсруэ, площадь которого составляет 70 000 кв. м. Объем склада достигает 760 000 куб. м, в его базе – 450 000 артикулов, мощность – до 17 500 отгружаемых позиций в день. Площадь склада в Карлсруэ составляет величину, равную 10 международным футбольным полям. Ежедневный объем – 200 контейнеров на отгрузке и приходе, и если составить башню из этих 200 контейнеров, то она будет высотой 518 метров, что выше Эйфелевой башни.Свечи зажигания. Технологии и тренды
К свечам зажигания предъявляют особые требования. Основа для их выполнения – практически полное отсутствие допусков при производстве, новые разработки в области материалов, геометрии, технологических процессов. На конференции были названы основные тренды данного рынка:
- уменьшение диаметра свечи, что дает больше возможностей для конструирования двигателя;
- увеличение длины резьбы;
- ужесточение требований к электрическим характеристикам свечи (к изолятору, керамике);
- применение более устойчивых к коррозии и искровой эрозии материалов и сплавов (интервал замены, превышающий 100 тыс. км.);
- направленный боковой электрод (в зависимости от типа двигателя определяются монтажный угол и положение свечей относительно инжектора).
При этом специалисты компании отмечают, что в будущем рынок свечей зажигания ждет застой. Причины кроются в увеличении доли дизеля, увеличении интервала между заменой свечей и в очень жесткой конкуренции.
Репортаж с производства Бамберг – Энгельс
Свечи зажигания – основной продукт компании с 1887 года, за все это время было произведено более 10 млрд свечей зажигания. В 1935 году Роберт Бош купил завод в Бамберге, а в 1940 году на заводе была произведена первая свеча зажигания. Завод в Энгельсе вошел в концерн в 1997 году и был полностью переоборудован. Стоит отметить, что производственные линии и в Бамберге, и в Энгельсе фактически идентичны, за исключением соотношения ручного и автоматического труда и количества типов свечей, выпускаемых на линиях.
Производство свечи зажигания проходит несколько этапов, на производство одной свечи уходит пять дней. Причина – долгое остывание и затвердевание керамической части (изолятора). В составе изолятора 59% глины. Смешивание глины с другими необходимыми материалами происходит в больших контейнерах. Все емкости полностью герметичны. После смешивания ингредиентов из порошка изготавливаются формы будущего изолятора. Допустимая норма усадки этой детали – 0,02 мм. Из 1000 экземпляров заготовок на соответствие размерам здесь проверяются пять, проверка производится при помощи лазерных технологий. После того как форма изолятора полностью готова, изделие отправляется в печь. На заводе в Бамберге расположено 46 газовых печей. Все они работают 15 лет без перерыва, т. к. после выключения привести печь в рабочее состояние можно лишь через 60 дней прогрева. Температура внутри – 1600 градусов, а допустимое колебание – всего 3 градуса. Керамические детали размещаются в специальных емкостях и отправляются в печь на сутки. После этого заготовка затвердевает, а размер ее сокращается до необходимых габаритов на 20%.
В соседнем цехе производят металлический корпус. Он делается методом холодного выдавливания из заготовки диаметром 13 мм. Это позволяет избежать лишних отходов (стружки), которые появились бы при использовании токарных станков. После нескольких этапов выдавливания корпус приобретает необходимую форму, затем к нему приваривают боковой электрод. На следующем этапе производства керамическую и металлическую части свечи соединяют и наносят последние штрихи перед упаковкой.
По официальным данным, около 20% выпускаемых на данном предприятии свечей идут на конвейеры мировых производителей. Остальные 80% — на свободный рынок. Завод в Бамберге работает в три смены по 7 часов. Доля ручной работы здесь минимальна: 90% действий производится в автоматизированном режиме. Основная функция людей – осуществлять визуальный контроль.
Свечной завод в Саратове
«Для меня невыносима мысль, когда при проверке моего изделия кто-нибудь смог бы доказать, что я сработал недоброкачественно и кое-как. Поэтому я постоянно старался работать так, чтобы моя работа выдержала любое важное испытание, была бы, так сказать, лучшей из лучших» (Роберт Бош, 1918 г.).
С этой цитаты начался последний день пресс-тура на ОАО «Роберт Бош Саратов» в городе Энгельсе, отделенном от Саратова примечательным мостом через Волгу длиной в 2,7 км. После короткой официальной части, которую провели руководитель производства Хорст Пельцер, заместитель директора по качеству Вячеслав Шикунов и региональный директор подразделения «Автозапчасти и диагностические оборудование» Олег Рябцев, состоялась экскурсия непосредственно на производственную линию, которую провели сотрудники предприятия Андрей Елецкий и Антон Носов.
Завод Bosch в России основан в 1997 году. Немецкая компания приобрела местное производство свечей и полностью модернизировала его. Единственное, что осталось пока от старой технологии, – печи, которые также вскоре будут заменены на новые, которые уже практически полностью установлены и вступят в эксплуатацию этим летом. Стоимость одной печи – 1,5 млн евро. Часть станков, установленных на заводе в Энгельсе, раньше работали на немецком заводе в Бамберге. Это не устаревшее или списанное оборудование. Как пояснил сотрудник Bosch, в Германии увеличивается доля автоматизированной работы, а в России более дешевая рабочая сила, поэтому покупать автоматические станки не всегда целесообразно. Немецкий завод Bosch поставляет в Россию сырье (гранулят, герметик, глазурь), центральные электроды, инструменты и калибры. Из Германии в Россию были перевезены высокотемпературная печь, пресс Hatebur, сварочные станки, резьбонакатный станок, авто- мат подгибки и просечки, линии сборки сердечника и линии окончательной сборки, а также упаковочные линии. Технологии завода Bosch в России позволяют делать свечи с одним, двумя или тремя боковыми электродами.
Материалы, из которых изготавливаются свечи в России, – те же, что и в Германии. Производство изолятора начинается с огромных «мельниц», в которых из глинозема и различных соединений получается зерно размером 2,5–3 микрона, а на втором этапе добавляются связующие компоненты. Получившиеся гранулы размером 50–70 микрон помещают в специальные канистры, в них смешивается горячий воздух и порошок, который распыляется внутри колбы. Готовая смесь заливается в формы. Четвертый этап – холодильная камера, после которой заготовки отправляются в печь и формируются там около 30 часов при 1600 гр. На заводе шутят: «Керамика – это без пяти минут алмаз». Сломать закаленный в печи изолятор невозможно. После обжига изоляторы проходят этап контроля.
На заводе работает несколько линий по изготолению сердечников (одни с резистором, другие – без него). Первый этап – сам изолятор, второй – его клеймение, третий этап – накатка ребрышек, четвертый – покрытие розовой глазурью. Затем в изолятор вставляется центральный электрод и засыпается герметик. Далее опять печь, где герметик становится жидким, глазурь расплавляется и происходит процесс герметизации.
Процесс создания металлической части свечи организован также, как на немецком заводе, – холодное выдавливание в несколько этапов. От токарных станков к новой технологии в Энгельсе перешли в 1999 году. Для контроля геометрической точности получаемой детали было приобретено несколько современных роботов и цифровых микроскопов. Полировка корпуса свечи проходит на таком же станке, как и в Бамберге. Для снижения уровня отходов на заводах Bosch организован замкнутый круг использования жидкости. В Энгельсе практически на всех этапах, где используется вода (например, для охлаждения детали), 95% ее возвращается на второй круг, 5% – испаряется. Поездка на производственные линии показала, что компания Bosch применяет одинаковые технологии при производстве свечей и в России, и в Германии. Единственное отличие между Энгельсом и Бамбергом в том, что в Энгельсе на некоторых участках линии используется ручной труд, в Бамберге же линии более автоматизированы.
Еще никто не оставил свои комментарии. Ваш комментарий будет первым.