Переход количества в качество
28 ноября 2012, Александр ФИЛОНОВ, Александр ШУБИН
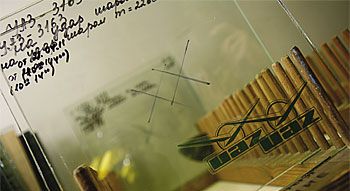
В начале этого года УАЗ объявил об увеличении гарантийного срока до трех лет или 100 тысяч километров пробега на автомобили UAZ Patriot, UAZ Patriot Sport и UAZ Pickup.
За скупыми строками этого информационного сообщения стоит большая организационная и техническая работа. Она началась много лет тому назад с исследований, выявивших влияние различных параметров на качество автомобиля. По заводским данным картина получилась такая:
Критерии, влияющие на качество автомобиля и их вес:
· 40 % – квалификация инженерного персонала;
· 30 % – качество комплектующих;
· 15 % – оснащенность необходимым сборочным оборудованием
· 14 % – мотивация рабочего персонала.
Работа по улучшению качества автомобиля велась по каждому из этих направлений, но нас сейчас будет занимать только одно из них, а именно: качество комплектующих. Одновременно проводилась работа по изменению бизнес-модели, которой предшествовали кропотливые изыскания, начатые еще в 2004 году, с началом выпуска «УАЗ Патриот». Результатом стал отказ от моделей, использующих нескольких поставщиков одной детали. Конечно, при этом заметно возрастают риски, как показали недавние события в Японии, но зато многократно облегчается управление качеством.
Из более чем 190 поставщиков сборочного конвейера в Ульяновске 70 % составляют отечественные производители. Именно на них и были направлены основные усилия.
Прежде всего, пятилетняя статистика работы с поставщиками дала возможность заводу произвести так называемую «интегрированную оценку поставщика». Интегрированная оценка – это набор индикаторов для определения соответствия поставщика установленным требованиям. Данные, позволяющие выполнить эту оценку, собирались как с помощью аудита при посещении предприятии поставщика представителями УАЗа, так и с помощью анализа результатов всевозможных предыдущих и настоящих контактов завода с поставщиком: периодичности и регулярности поставок, качества продукции и его стабильности, то есть всех сведений об их деятельности. Эти сведения собирались людьми, которые административно не были связаны между собой, работали в различных департаментах УАЗа: департаменте закупок, департаменте обеспечения производства, департаменте обеспечения качества, департаменте развития поставщиков. Такая организация сбора данных гарантировала большую объективность результатов. Документация для определения данных, входящих в интегральную оценку поставщика, и требований к конкретному потребителю была разработана на основе стандартов ISO и ряда других международных нормативов.
Согласно данным «интегрированной оценки поставщика» все поставщики были разделены на категории и каждому из них присвоен свой статус.
С поставщиками, получившими высшую оценку, было рекомендовано продолжать работать, с поставщиками, получившими низкую оценку, работать было не рекомендовано, а с «середнячками» работа допускается при проведении ими ряда мер, улучшающих продукцию, и под ежегодным аудитом и постоянным мониторингом со стороны покупателя продукции, то есть УАЗа. Таким предприятиям выставляются дополнительные требования, в случае выполнения которых их интегральная оценка может быть повышена.
Критерии отбора поставщиков и требования, предъявляемые поставляемой продукции, были сформулированы предельно точно.
Поставщик должен в ближайшее время выполнить сертификацию своего предприятия по ISO, (если ее еще не было сделано до этого). Обеспечить полное отсутствие дефектов при проведении входного контроля у потребителя. Более того, поставщик должен гарантировать возможность использования поставляемого товара вообще без входного контроля у покупателя.
Суммарный уровень дефектов, выявленный при входном контроле, производстве и эксплуатации, должен быть не более 50 ррм (50 дефектов на 10000 единиц поставляемо продукции), а гарантийный срок на комплектующие равен гарантийному сроку на автомобиль.
Поскольку не все поставщики смогли на 100 % соответствовать требуемым критериям, то они согласно интегрированной оценке были разбиты на категории A, B, C, D. Соответственно, отличный, хороший, удовлетворительный и неудовлетворительный.
C тех пор, как поставщиков «посчитали», то есть точно определили степень соответствия из продукции предъявляемым требованиям, с ними стали вести планомерную работу, направленную на увеличение доли поставщиков категории А и В и постепенное снижение доли продукции поставщиков С и D, а по возможности вообще исключения последних из списка поставщиков и замены поставляемой ими продукции на более высококачественную.
Так, если в 2007 году поставщиков категории А и В было всего 47 %, то в 2010 году их стало 70 %, и это число продолжает расти.
Вся эта работа стала одной из причин объективного увеличения качества автомобилей УАЗ. Объективного, то есть подтвержденного такими показателями, как удельная дефектность комплектующих (снижена за год на 12 %) и удельная рекламационная деятельность (по серии Patriot снижена в 5,3 раза по сравнению с 2009 годом).
Собственно говоря, эти цифры и привели к появлению решения, о котором сказано в самом начале, – к увеличению срока гарантии.
При этом завод не остановился на достигнутом. Разработана так называемая «политика взаимодействия» с поставщиками, в рамках которой ведется многогранная и многопрофильная работа по выявлению несоответствия продукции предъявляемым требованиям и устранения дефектов.
Все это еще более поднимает качество выпускаемых автомобилей и позволяет им достойно конкурировать с продукцией ведущих западных фирм.
Можно привести несколько примеров предприятий, которых УАЗ выбирает себе в поставщики.
Пример №1
Входящий в состав AGC Group Asahi Class Company Борский стекольный завод поставляет на конвейер Ульяновского автомобильного завода 7 видов стекол (предназначенных для остекления кузова).
Статус поставщика – отличный. В 2010 году дефектов поставленной продукции не выявлено вообще.
AGC Group Asahi Class Company – крупнейший в мире производитель стекла. Компания работает в 30 странах мира, охватывает 45,5% мирового рынка стекла. В распоряжении компании 18 флоат-линий, 6 линий по производству автомобильного стекла и более 10 производственных подразделений.
AGC – ведущий поставщик стекла для строительной, автомобильной и электротехнической отраслей. Бизнес построен таким образом, что потребитель в каждом из регионов получает продукцию, соответствующую требованием конкретного рынка.
Штаб-квартира подразделения AGC Glass Europe расположена в Бельгии.
В Европе производится флоат-стекло, которое применяют в строительстве и автомобильной промышленности. Компания предлагает продукцию, имеющую лучшие показатели по всем важнейшим характеристикам.
Автомобильное стекло AGC – это комплектующие для рынков ОЕМ (автозаводов) и ARG (запасных частей). В ассортименте компании есть как закаленное стекло, так и триплекс, а также стекла для общественного транспорта и стекла для автомобильных осветительных приборов. В ассортименте компании представлены теплоизолирующее зеленое стекло и ветровое стекло с токообогревом. AGC поставляет стекла для заводов АвтоВАЗ, ГАЗ, УАЗ, Toyota, Ford, Renault, Volvo, Mitsubishi, Honda, Nissan, BMW, VW Group и других.
Начиная с 1997 года компания начала бизнес в России, поэтапно приобретая Борский стекольный завод, и, построив с нуля производственный комплекс в Клину. (Это первый в России завод, построенный на пустом месте западной компанией). В Клину уже работает крупнейшая в мире линия по производству флоат-стекла – проект «Клин-2».
Борский стекольный завод – это первое российское предприятие стекольной отрасли, модернизированное с учетом современных технологических требований. Сегодня на предприятии работает две современные флоат-линии общей производительностью более 1200 тонн листового стекла в сутки.
Завод оснащен новейшим оборудованием по производству закаленного стекла. Три линии по выпуску триплекса и линия по производству закаленного стекла позволяют производить более 1,4 млн машинокомплектов в год. Предприятие оснащено уникальной, не имеющей мировых аналогов печью для выпуска мелкосерийных партий стекла для рынка запасных частей.
70 % автостекла для комплектации автомобилей, собираемых в России, произведено компанией AGC.
Автомобильное стекло – это один из приоритетов AGC Glass Russia. Управляющий центр автомобильного стекла для автопроизводителей расположен в г. Бор Нижегородской области. Направление автомобильного стекла для рынка запасных частей имеет пять дистрибуционных центров в Москве, Санкт-Петербурге, Нижнем Новгороде, Ростове-на-Дону и Екатеринбурге. Кроме того, компания развивает сеть центров по замене автостекла, работающих под брендом AG Expert. Уже открыты 17 центров: в Москве, Санкт-Петербурге, Нижнем Новгороде, Самаре, Тольятти и Ростове-на-Дону.
AGC создает два центра дооснащения автомобильного стекла (Added Value Operations) для обслуживания сборочного завода Toyota в Колпино и для широкого круга автопроизводителей в г. Бор.
На всех предприятиях AGC в России внедрена комплексная система менеджмента качества, профессиональной безопасности и охраны окружающей среды, основанная на стандартах ISO 9001, ISO 14001, OHSAS 18001.
Пример №2
Компания Bosch поставляет на конвейер УАЗ весьма широкий спектр комплектующих по следующим направлениям:
- система рулевого управления
- автомобильная электроника
- мультимедийные системы
- электрические приводы
- бензиновые системы
- система контроля шасси
- тормозные системы
- дизельные системы
- стартеры и генераторы
- запасные части.
Хотя большинство комплектующих на данный момент поставляется из Германии, компания продолжает стратегию по локализации производств. Уже на сегодня немалую роль играет успешно действующее уже полтора десятилетия в г. Энгельсе ОАО «Роберт Бош Саратов». Что знаменательно, 15-летний юбилей предприятия совпал с 125-летним юбилеем компании.
В 1997 году «Роберт Бош ГмбХ» приобрел контрольный пакет акций открытого акционерного общества с иностранными инвестициями «Завод автотракторных запальных свечей» и переместил из Саратова на его территорию в Энгельс производство компонентов электронного впрыска топлива. В 1998 году на ООО «Бош-Саратов» начата сборка блоков управления, и с этого момента практически каждый год ассортимент продукции завода пополнялся. В частности, 2010 год ознаменовало начало производства изделий соединительной техники, более 100 новых типов свечей для рынка Европы и США, а в текущем начато производство топливных насосов высокого давления.
На сегодняшний день на современном производственном оборудовании предприятие выпускает автокомпоненты как для российской, так и для международной автомобильной промышленности: свечи зажигания, датчики массового расхода воздуха, датчики кислорода (лямбда-зонды), блоки управления, модули центрального моновпрыска, модули бензонасоса, моторные жгуты проводов, топливные рампы.
Выпуская компоненты для 15 различных брендов, предприятие поставляет их не только в пределах нашей страны, но и активно экспортирует в США, Великобританию, Испанию, Португалию, Ближний Восток, Китай, ЮАР, Индонезию, Тайвань, Филиппины, Латинскую Америку и даже Австралию с отметкой «Made in Russia».
Предприятие сертифицировано по стандартам ISO 9001 и ISO/TS 16949.
Особенностью деятельности предприятия (естественно, отличающей его от отечественных, а не от входящих в концерн Bosch) является система Bosch Production System, обеспечивающая поставку правильной деталь в необходимом количеств в необходимый момент с необходимым качеством в необходимом месте.
Отклонение производства и в меньшую, и в большую сторону считается признаком нестабильности процесса, неизбежно ведущей к потерям.
Если попытаться описать систему «на пальцах», то она действует «задом наперед», или, как здесь называют, «втягиванием». Скажем, если со склада изъято определенное количество изделий для поставок заказчику, там образуется «вакуум», который начинает «всасывать» новые изделия с конвейера. Соответственно, конвейер начинает «всасывать» необходимые детали с промежуточного склада и т. д. Таким образом, на всех этапах обеспечивается бесперебойная работа, гибко перестраиваемая в зависимости от текущей ситуации.
Дополнительно гибкость обеспечивается и специфической планировкой конвейера, работу которого можно перестраивать в зависимости от изделия и числа доступных работников.
При этом все технологические этапы, где вмешательство человека не требуется или даже нежелательно, как при производстве топливной рампы, полностью автоматизированы.
Отдельно необходимо упомянуть о контроле качества, осуществляемом с использованием автоматизированных диагностических устройств, распечатывающих для каждого изделия контрольный талон с указанием времени прохождения контроля, соответствия параметров заданным и т. п.
Дополнительной мерой обеспечения качества служат также регулярные аудиты, проводимые как представителями самой компании Robert Bosch Gmbh, так и компаний-партнеров и клиентов.
Еще никто не оставил свои комментарии. Ваш комментарий будет первым.