Планирование производственных процессов
2 декабря 2014, Александр АНАНСОН, Анастасия ПУШКИНА
Тема планирования – одна из самых обсуждаемых на любом производстве. Казалось бы, столько внимания этому уделено, что все решения найдены и никаких проблем по этой части существовать не должно. Однако даже на крупных авторизованных станциях нередки ситуации, когда планы срываются, выход автомобиля задерживается, а нерешенные проблемы, как ком, начинают нарастать и сбивать все планы. Итак, еще раз о планировании производственных процессов…
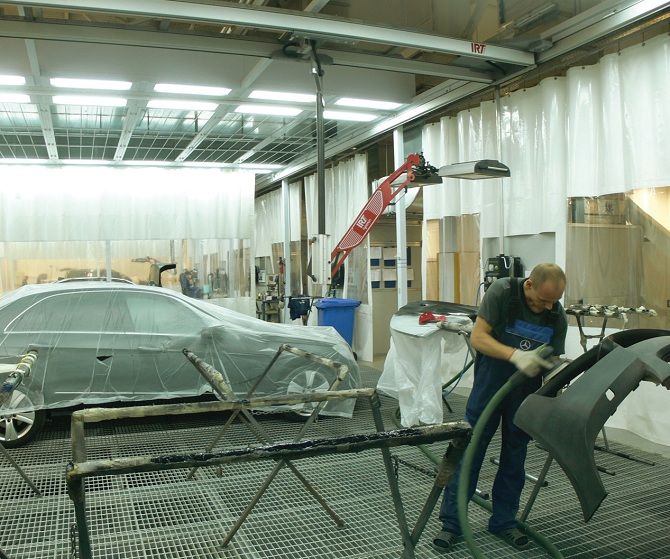
Если сравнивать планирование кузовного и слесарно-механического цехов, то мы увидим, что процессы работы в этих производствах различны. В слесарно-механическом цеху весь ремонт выполняется на одном рабочем месте, поэтому ситуация достаточно прозрачна и планирование не вызывает особых затруднений. В редких случаях работы выполняются на разных постах, например, это пост шиномонтажных работ, развал-схождение и подъемник. Как правило, заполняются три отдельных заказ-наряда (в случае работы с одним и тем же автомобилем на разных постах). В кузовном цеху цикл прохождения автомобиля по всем постам и будет одним заказ-нарядом. Планировать и отслеживать работу сложнее. Так, один пост может тормозить все производство. Или, если у поста большая проходимость, он будет загружать все производство и тем самым также нарушать ритмичность загрузки. Здесь, как и в любом деле, важен баланс, который можно достичь разумным планированием.
Парадоксально, но в большинстве автосервисов можно встретить ситуацию, при которой все планирование кузовного производства происходит в головах мастера-приемщика и мастера производства. Они просто помнят, где какая машина размещается и на какой стадии ее ремонт. Это оборачивается суперзависимостью сложного производственного цикла от одного человека. Стоит ему что-то выпустить из внимания, и работа всех подразделений может выйти из-под контроля. Поэтому зафиксированное каким-то образом планирование, к которому в любой момент могут обратиться ключевые специалисты производства, принципиально важно. Оно также позволяет анализировать показатели эффективности и принимать стратегические решения, устранять «узкие места» и выявлять дополнительные возможности для получения прибыли. Из практического опыта работы в направлении консалтинга можно добавить, что нереализованные возможности кузовного производства и скрытые проблемы, связанные с эффективностью производства, кроются зачастую именно в планировании.
Какие решения и инструменты для планирования существуют на сегодняшний день? Рынок узкопрофессионального программного обеспечения предлагает разные решения для этой задачи. Профессионалы хорошо осведомлены о различных программах, которые достаточно точно описывают процессы на предприятии, фиксируют данные об отдельном автомобиле, заказ-наряде, проводят процессы заказа запчастей и т. д. Однако самый большой их недостаток в том, что они не позволяют видеть срез по производству здесь и сейчас. Возможно, это отчасти связано со спецификой кузовного производства и с тем, что в программное обеспечение не закладываются логика и последовательность его работы.
Если говорить о ядре идеального программного продукта, то в общих чертах это объемный органайзер, в котором отражена планируемая и текущая загрузка каждого из постов.
Можно привести примеры некоторых кузовных производств, которые достаточно успешно решают вопросы планирования с помощью популярных широко используемых офисных программ с функциями календаря. Например, это различные почтовые программы, с которыми удобно работать в сети, где возможно разделять задачи по времени и строить графики на каждый день. Основные требования к ним – это способность работать в онлайн-режиме с несколькими пользователями. С помощью одновременного доступа график загрузки могут видеть мастер-приемщик, мастер производства, специалисты отдела запасных частей и, конечно, руководитель.
Другой пример – физическая доска загрузки, на которой отражается движение заказ-наряда. В общем случае на доске загрузки столько ячеек, сколько постов в цеху. Мастер производства перемещает заказы на доске загрузки в соответствии с продвижением автомобиля по постам.
Такое отражение реального положения дел в цеху очень помогает контролировать работу, но и у этого варианта есть свои минусы. В основном это касается удобства пользования, ведь мастеру цеха необходимо постоянно подходить к доске, чтобы свериться с ней. Кроме того, доска загрузки не очень удобна для совместной работы нескольких специалистов.
Чтобы подобраться к идеальному инструменту планирования производственных процессов, попытаемся разобраться в целях и задачах, которые он должен решать.
Инструмент планирования должен быть удобен для использования основными специалистами, которые и составляют эти планы: мастером-приемщиком, мастером производства и специалистом отдела запасных частей. Удобен – значит должен учитывать особенности работы этих специалистов и отвечать выполняемым ими функциям.
От мастера-приемщика зависит загрузка производства и время выдачи отремонтированного автомобиля, а от мастера цеха – выполнение ремонта. Взаимодействие этих служб, пожалуй, определяющий фактор для нормальной работы цеха. Принимая автомобиль в ремонт, мастер-приемщик должен очень точно представлять себе текущую ситуацию на производстве и знать, где и какие «окна» для загрузки имеются. Мастер производства должен своевременно обозначить возможности для загрузки, а также контролировать выполнение уже подготовленного графика работ. Очень важно в этот процесс включить взаимодействие с отделом запчастей. От этого зависит время, когда машина поступит в производство. Основная функция выполняется на этапе подготовки к ремонту, но не стоит забывать, что и в момент ремонта, если выявляются скрытые дефекты и необходимость дополнительного заказа запчастей, скорость поставки необходимого оборудования напрямую влияет на срок выдачи автомобиля клиенту.
За пределами непосредственного взаимодействия служб станции находится топ-менеджемент. Однако планирование рабочих процессов для руководителя ничуть не менее важно, чем для ведущих специалистов. Руководитель должен видеть состояние производства «в масштабе», постоянно анализировать эффективность рабочих постов и загрузку работников, реагировать на сбои в планировании и вовремя принимать стратегические решения. Все это позволяет выполнить грамотное планирование.
А теперь смоделируем обычную рабочую ситуацию в любом автосервисе и обозначим, как должно быть реализовано оптимальное планирование кузовного производства. Рабочий процесс начинается с мастера-приемщика. Клиент задает ему два основных вопроса: сколько будет стоить ремонт и когда можно будет забрать автомобиль (наши автовладельцы, как правило, не очень требовательные и не берут подменную машину на время ремонта). Чтобы ответить на эти два вопроса, мастер-приемщик, во-первых, должен провести диагностику автомобиля, уточнить калькуляцию, полученную от страховой компании. В этом вопросе ему помогают множество программных решений (многие реализованы на базе «1С: Бухгалтерия»); как правило, эти моменты проходят по обкатанной схеме и без особых затруднений. А вот чтобы ответить на второй вопрос, мастер-приемщик должен снестись с мастером производства, выяснить, когда и где есть возможность отремонтировать автомобиль и какой специалист сможет взяться за эту работу. По сути, главное – узнать, когда автомобиль зайдет в цех, тогда можно предположить, когда он выйдет. При этом отдел запасных частей должен предоставить информацию, когда и какие запчасти будут в наличии и когда ремонт будет укомплектован всем необходимым. То есть мастер-приемщик должен свериться с двумя службами: производством и отделом запчастей – и только согласовав с ними все вопросы, он может уверенно ответить клиенту о сроках готовности авто.
Именно из-за плохой согласованности служб возникают ситуации, когда машина с мелкой царапиной на бампере выходит из ремонта через месяц.
Мастер цеха, который принял машину в ремонт, должен контролировать ее своевременное продвижение по всем постам и оперативно вносить изменения в график, если вдруг возникают непредвиденные затруднения. Что говорить, случаются и непредвиденные накладки и сбои в процессах из-за человеческих факторов, но они не должны рушить всю систему планирования. Если мастер упустил из виду изменения в графике, приходится хранить автомобиль в цеху и ждать запчасти, материалы или специалиста, отодвигается срок выдачи автомобиля клиенту, и по нарастающей одна проблема может потянуть за собой гораздо большие неприятности.
Куда проще управлять ситуацией, если у мастера-приемщика есть график дня с определенными интервалами, а мастер производства оперативно его редактирует. Этот график «живой» и является инструментом для быстрого реагирования. В принципе, не столь важно, в каком виде он будет реализован: как программа, доступная на стационарном компьютере или КПК, или как график в единой тетради учета. Конечно, последний вариант смешнее: «вчерашний день», но тоже работает. Принципиально важно реализовать действительный порядок взаимодействия специалистов: мастер-приемщик может вносить в график работы, но не может его редактировать, а мастер производства должен оперативно редактировать график в соответствии с реальным положением дел, но не вправе что-либо удалять.
Казалось бы, что эти предложения стары как мир и очень просты. Наверное, именно эта простота и побуждает к тому, чтобы держать всю эту информацию в голове. Однако если через ваш цех проходит 200 машин в месяц, то простота исчезает. Грамотное планирование поможет всегда быть хозяином положения и выполнять обещания, данные клиентам.
Комментарии
Рекомендованные статьи
Еще никто не оставил свои комментарии. Ваш комментарий будет первым.