Шик, блеск, красота...
17 декабря 2014, Евгений МАГАКОВ
Зададимся вопросом: чем существенно отличается реставрационный процесс двух похожих по периоду изготовления ретроавтомобилей – например, кабриолета «Москвич 400» и ГАЗ-67?
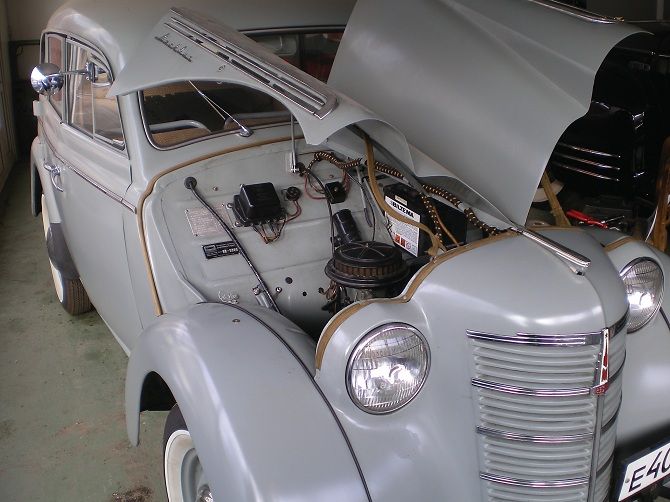
Догадливый читатель найдет общность моделей в следующем: тент, одинаковая компоновка агрегатов, но вот что начисто отсутствует в перечне работ с «Иван-Виллисом», так это восстановление хромированных деталей, ибо их там отродясь не было.
Неявная, на первый взгляд, разница дает экономию по работам до 7000 долларов, а вот на чем набирается указанная сумма, станет понятно по прочтении данной статьи.
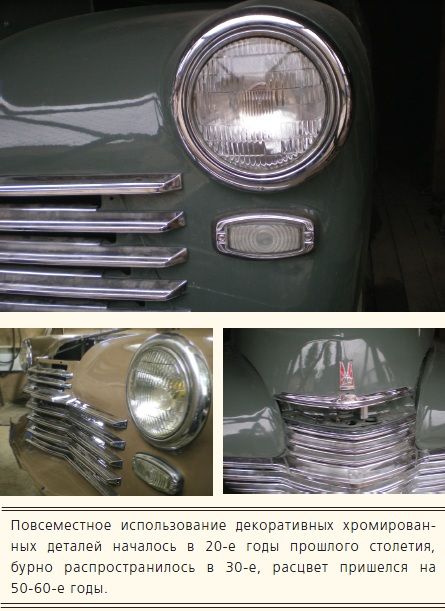
Первые детали, покрытые гальваническим способом, появились в автостроении вовсе не из-за любви к красоте, а для качественной защиты их от коррозии. Повсеместное использование декоративных хромированных деталей началось в 20-е годы прошлого столетия, бурно распространилось в 30-е, расцвет пришелся на 50-60-е годы, обилие хрома на американских «дредноутах» и сегодня поражает воображение. Вот только создать заводскую модель для массового производства на конвейере и воссоздать ее после десятков лет забвения – совсем не одно и то же. И хотя принципы реставрации предусматривают точное соблюдение конструкции и заводских технологий, нынче найти источник свежего хрома – непростая задача. С одной стороны, надо расхромировать все и вся, придать всем деталям требуемую, но, увы, утраченную форму, восстановить проржавевшие насквозь участки и по технологии нанести медь-никель-хром для обеспечения долгого срока службы детали в новых условиях. А для того чтобы правильно нанести все указанные покрытия, надо обладать гальваническим цехом из 15–17 ванн, достаточно вместительных, чтобы детали можно было погрузить в них целиком, да еще с промежуточной промывкой в ваннах с дистиллированной водой, достаточными мощностями для питания трансформатора и т. д. С точки зрения экологической вредности подобные производства весьма опасны для окружающей среды, да еще и крайне энергоемки. Подавляющее количество заводов, где в советское время гальванические производства были в избытке, постепенно закрылись или перепрофилировались, после демонтажа оборудование не смонтировали на других площадках, и оно пришло в негодность под воздействием погодных условий и благодаря усилиям мародеров. Оставшиеся «в теме» производства крайне неохотно берут в работу разовые заказы частников, ведь, кроме окунания в ванну, надо проводить промежуточное шлифование и полировку получаемых слоев, а также финишную полировку. И это все касается абсолютно ровных деталей облицовки радиатора, бамперов, ручек и пр.
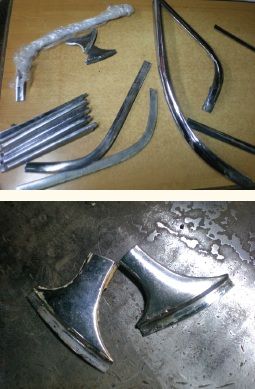
Металла в свое время не жалели, толщина проката для изготовления бампера ЗиМа ГАЗ-12 доходила до трех миллиметров, мелкие дефекты можно устранить простой шлифовкой абразивами. Параллельно надо рихтовать жестко закрепленную деталь, устраняя перекосы и вмятины. Часто приходится рассверливать и заваривать глубокие каверны с последующей шлифовкой, вваривать новые крепежные элементы и даже собирать конструктор из нескольких однотипных деталей. Проблема состоит именно в тщательности шлифовки, подборе зернистости абразивов, качестве сварного шва (он не должен иметь пор и непроваров), в сохранении геометрии ребер, стыков и краев детали. Испортить на наждаке вполне восстановимый колпак – пара минут, исправить халтуру подчас невозможно…
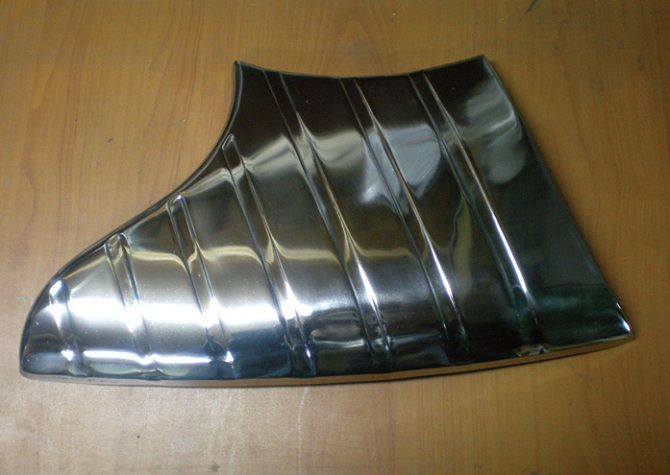
Предположим, что все стальные детали из набора хромированных элементов кузова и салона мы подготовили, но теперь надо заняться латунными молдингами и накладками. Их подготовка осложняется наличием усталостных трещин, окислением и малой толщиной, сошлифовать в случае необходимости дефект не получится. При необходимом снятии старого покрытия применение электрохимического способа может испортить деталь, ее «ведет» и деформирует в ванне, поверхность «подгорает», а при механическом снятии с тонкой детали старого хрома можно нарушить четкость линий и превратить кромки в бритву или, наоборот, ребра в овалы. Пайка в процессе ремонта тоже несет в себе много проблем: неправильно положенный шов предательски изменяет цвет на отхромированной поверхности, как говорится в одной рекламе: «иногда следы ремонта видны».
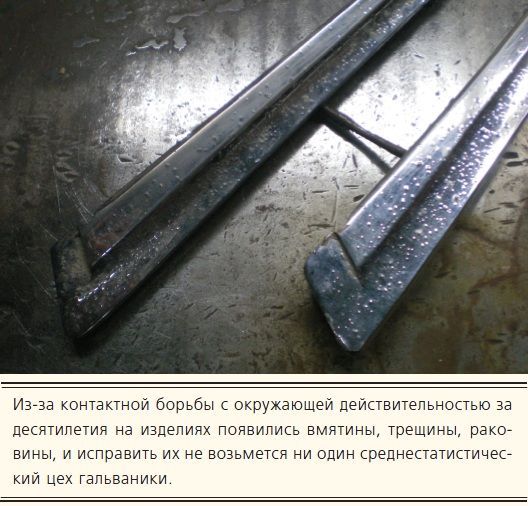
Наконец мы подошли к самой трудной задаче – восстановление деталей из цинк-алюминиевого сплава, еще именующегося ЦиАМ. Это ручки наружные и внутренние, молдинги, корпуса фонарей и эмблем, элементы облицовки фальшрадиатора, надписи и шильдики. Тут уже все вышеперечисленные проблемы встают в полный рост, так как силумин может запросто раствориться в ванне расхрома, лопнуть при меднении, а корродирует поверхность под слоем хрома вглубь с образованием глубоких пор, и простой шлифовкой ее не убрать. Иногда проще и быстрее изготовить точную копию-отливку из латуни и отхромировать ее с подготовкой, чем пытаться сгладить дефекты родной детали, в итоге испортив ее окончательно и бесповоротно. Яркий пример такой проблемы – корпус фонаря подсветки заднего номера ГАЗ‑21 (именуемая в народе за характерную форму «птичка багажника»), имеющий толщину всего около миллиметра и множество острых граней, но покрывающийся за время службы обильными высыпаниями и язвами.
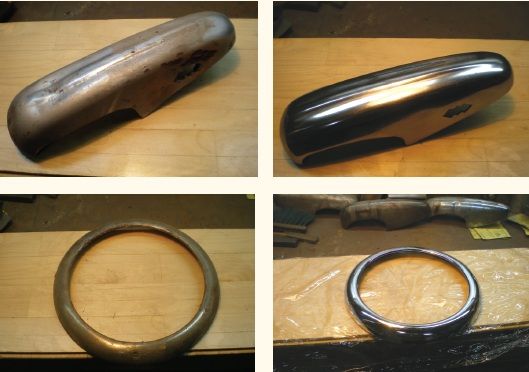
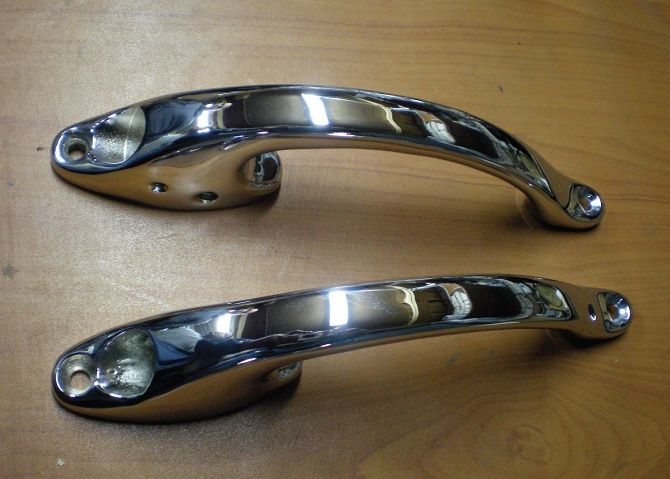
И даже победа над геометрией детали, когда в ходе достигнута идеальная поверхность, – это половина задачи. Теперь нельзя допустить нарушения технологического цикла нанесения всех необходимых слоев покрытий, так как на сталь нельзя сразу наносить хром или никель. По аналогии с окраской, где металлу жизненно необходим грунт для надежного сцепления с краской, а еще лучше два типа грунта (антикоррозионный и поронаполнитель), в нашем случае роль антикоррозионного слоя выполняет медь. Ее же можно шлифовать и добиваться разглаживания мелких дефектов поверхности за счет заполнения пор и мелких кратеров, наносить снова для увеличения толщины и снова шлифовать. Потом наносится слой никеля, а уж только потом хром толщиной всего в несколько микрон. Именно хром дает нужный оттенок (сам никель имеет желтоватый тон) и работает как электрохимическая защита никеля, так же как и нанесение лака дает защиту ЛКМ и увеличивает визуальный эффект, дает «глубину» и усиливает блеск покрытия. Последняя стадия – полировка изделия, снова полная аналогия с покраской, где применяются абразивные пасты для тончайшего шлифования поверхности, придается блеск и глянец.
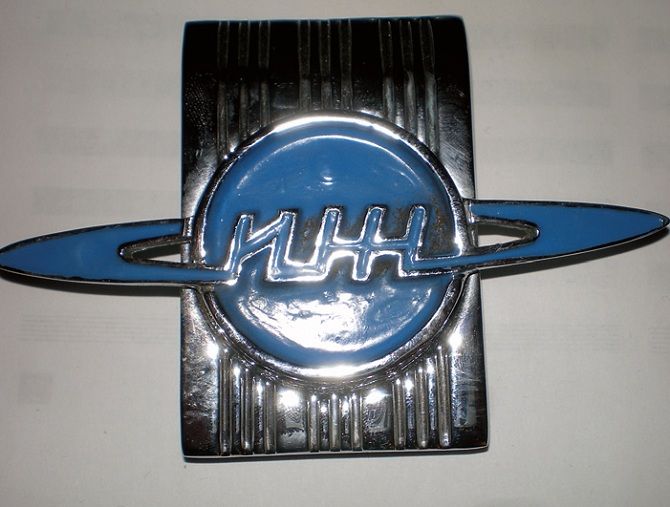
Не стоит забывать, что технологический цикл гальванического нанесения может полностью перечеркнуть работу подготовщика из-за неправильного выбора режима нанесения, ошибочного подбора тока, температуры раствора в ванне, плохого обезжиривания и промывки в дистиллированной воде между окунаниями в разные ванны. Часто доводилось держать в руках детали после неудачной хромировки, испорченные из-за мусора и шлама в ванне, плохо промытые, со следами крепления к держателям и пр.
Вот почему данная технологическая операция обходится очень недешево при комплексной реставрации и доставляет столько хлопот. Пожелаем читателю избежать описанного негатива, получить свои детали в срок, в полном объеме и отличного качества, но, как говорится, кто предупрежден – тот вооружен!
Комментарии
Рекомендованные статьи
Еще никто не оставил свои комментарии. Ваш комментарий будет первым.