Сочная тяга к «баваркам»
14 марта 2016, Роман АКОЛЬЗИН
Зимний тест для редакции ознаменовался знакомством с BMW 320d xDrive. В столь холодные и снежные месяцы мы специально остановили наше внимание на дизельной версии, чтобы выяснить, насколько требователен и ремонтопригоден автомобиль в условиях российской зимы. Наши постоянные эксперты от концерна ZF и технического центра «Юнит» помогли журналу разобраться в этом вопросе.
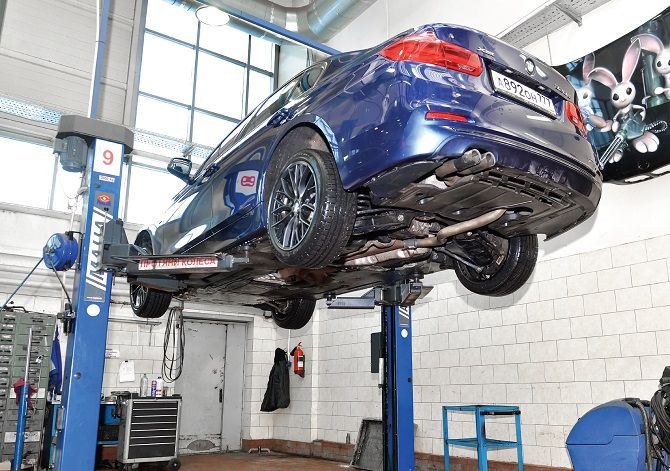
190-сильная (140кВт) «трешка» вооружена N47D20 – 4-цилиндровым дизельным мотором BMW TwinPower Turbo объемом 2,0 литра. Одно время из-за сумятицы с терминами в сети преобладала информация, что лошадиные силы с этого ДВС снимают сразу две турбины.
Ошибка закралась из-за названия TwinPower Turbo, которое у потребителя четко ассоциировалось с баварским понятием Variable Twin Turbo. Эта технология, применяемая в некоторых дизельных двигателях BMW, действительно предусматривает последовательную установку двух турбокомпрессоров: в зависимости от оборотов попеременно или вместе задействуются малая и крупная турбины. Такой заводской тюнинг позволяет максимизировать КПД при любой скорости и нагрузке.
В обсуждаемом же моторе 2.0 турбонаддув исполнен в виде системы Twin-scroll, что подразумевает работу одного компрессора под действием двух турбовентиляторов, установленных в каналах для выхлопных газов. С идеологической точки зрения технология идентична Variable Twin Turbo. Ее основная задача – также ускоренно нагнетать и повышать давление в системе. Однако система Twin-scroll компактнее, дешевле и легче аналога. В общем, TwinPower Turbo – это одна турбина с изменяемой геометрией двойной крыльчатки, работающая в совокупности с высокоточной системой непосредственного впрыска Common Rail. Гибкая электронная система управления корректирует фазу и дозировку впрыскиваемого топлива в соответствии с рабочей температурой, давлением в цилиндре и требуемой мощностью. Пьезоинжекторы впрыскивают топливо несколько раз за один рабочий такт, затрачивая всего 0,27 миллисекунды. Улучшенное внутреннее охлаждение камеры сгорания в процессе прямого впрыска позволяет применять сверхвысокую степень сжатия, снижая расход солярки.
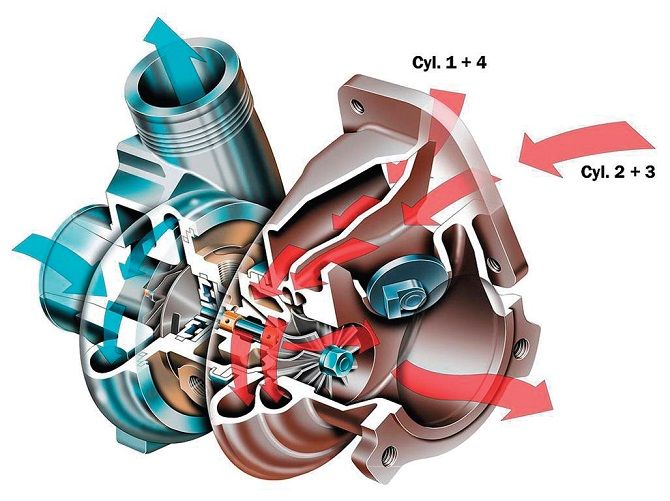
По информации Александра Егорова, генерального директора технического центра «Юнит», на дизельные «трешки» приходится 7-8% потока обслуживаемых автомобилей. Столь малый показатель говорит о высокой надежности моторов BMW. Однако эксперт все-таки сетует на даунсайзинг, который вносит свои печальные коррективы, ведь чем компактнее детали, чем сложнее их конструкция, чем больше их сопряжено в одном месте, тем меньше ресурсность. «С годами дизель стало намного проще обслуживать. Канули в лету плунжерные насосы и сложные механические настройки, появились электронные системы впрыска. Проще заказать новый законченный элемент, нежели менять распылитель на электронной форсунке. Предварительно они легко диагностируются на партнерских дизель-сервисах Bosch», – рассказывает Александр.
Основная проблема N47D20 – навесное оборудование. Демпфер крутильных колебаний, призванный снижать вибрации ДВС, со временем приходит в негодность. Верхний резиновый слой истончается и рвется, после чего слетают обод шкива и ремень навесного оборудования. Поломку легко спрогнозировать, периодически осматривая демпфер, или заметить по усилившейся вибрации. Таким же образом выходит из строя муфта карданного вала.
Стоит обратить внимание на цепь ГРМ, которая растягивается к 100 000 км пробега и начинает неприятно звенеть. Однако самое печальное, что на это нельзя долго закрывать глаза, как в случае с другими цепными ДВС. Цепь быстро изнашивается и вытягивается до критического уровня, после чего одно из звеньев разрушается. Также может выработать свой ход натяжитель. В итоге цепь перескочит на шестерне, валы рассинхронизируются, и поршни загнут клапаны.
Зато с турбиной на дизеле проблем не будет никаких. В бензиновых моторах из-за перегрева каналы подачи масла в турбине постепенно закоксовываются. При принудительной остановке ДВС масляный насос и вовсе перестает прокачивать масло через них. Оно моментально вскипает и пригарает. Забитые каналы не позволяют в дальнейшем смазывать и снимать температуру с турбины, что приводит к поломке подшипника. Средняя рабочая температура дизеля заметно ниже. Он не боится пробок и длительного холостого хода. За счет низкого тепловыделения и холодного выхлопа турбина совершенно не перегревается. Отпадает необходимость в установке турботаймера.
Эксперты уверяют, что даже на не самом лучшем масле мотор спокойно пройдет более 250 000 км. И только после этого рубежа с ним могут возникнуть проблемы, которые присущи бензиновым двигателям с 50 000 на одометре.
Ну, а самая знаменитая проблема N47D20 – это система по уменьшению выбросов окислов азота в атмосферу. Российское топливо и сложный климат приводят к преждевременному загрязнению системы. Чтобы избежать проблем с забитым сажевым фильтром, клапаном рециркуляции и вихревыми заслонками, российские «кулибины» к 150 000 просто избавляются от них. Процедура недешевая и потребует кодирования. Некоторые тогда же чипуют свои машины, но, по мнению наших экспертов, в случае с дизелем это катастрофически влияет на ресурс.
На 320d установлен доработанный вариант восьмиступенчатой АКПП ZF 8HP45. Это очень известный «спортивный автомат», который в модификациях также устанавливается на Chrysler и переднеприводные Audi. «Сейчас поставляются в серию 8-ступенчатые АКПП второго поколения, это очень надежные и экономичные по топливу агрегаты. Коробка прощает многие ошибки и проблемы эксплуатации, стиля вождения, дорожных условий. При надлежащем обслуживании эта АКПП не выходит из строя, как в гарантийный, так и в постгарантийный период. В блок управления агрегата «залито» 27 программ, и автомобиль сам, без участия водителя, выбирает оптимальную. Например, для движения по заснеженной дороге с пробуксовкой, для движения в гористой местности и т. д. Программы формируются на стадии проектирования и тестирования АКПП и конкретных моделей автомобиля, с участием инженеров и водителей-испытателей концерна ZF. С 2016 года 8-ступенчатые агрегаты будут приниматься в ремонт нашим центром ремонта и восстановления, все технологии, компетенции и запчасти для этого имеются. Можно уже сейчас сказать: в ремонте и восстановлении эти АКПП более экономичны, чем 6-ступенчатые, они в своей конструкции не имеют явных слабых мест, и их конструкция базируется на принципиально иной технологической концепции. Если что-то в этих АКПП выходит из строя, как правило это вследствие естественного износа», – рассказал в интервью Олег Молотков, генеральный директор ООО «ЦФ Руссия», дочерней фирмы концерна «ZF Friedrichshafen AG».
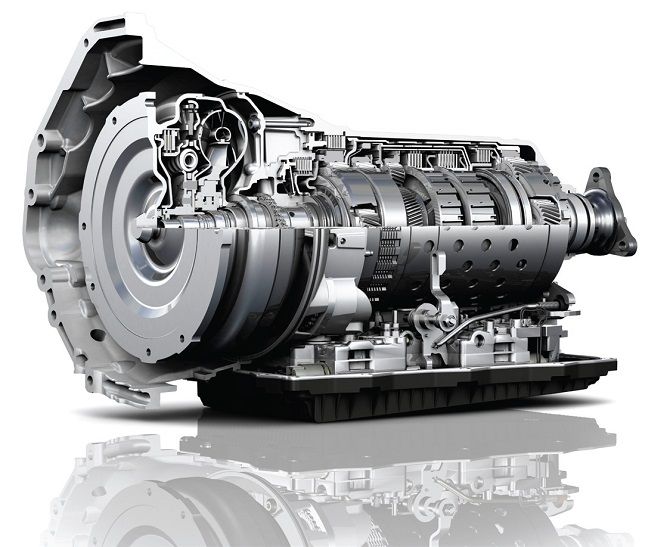
В сравнении с прошлой серией (6HP) новая коробка существенно усложнилась, но при этом стала надежнее. В конструкции передачи настолько сближены, что переключения происходят с незаметной потерей потока мощности в 200 миллисекунд. Это настоящий вызов DSG. Достается и вариаторам, ведь соленоиды здесь работают все вместе, позволяя очень плавно переключать передачи даже в агрессивных режимах.
Заслуживает внимания гидравлическая система управления. При малых оборотах двигателя гидротрансформатор блокируется, что приводит к снижению расхода топлива и повышению КПД мотора. Когда машина находится в неподвижном состоянии, а ДВС работает на холостых, коробка автоматически переходит на «нейтралку». В жаркую погоду в угоду климат-контролю система предпочитает пониженные передачи, в холодную – повышенные для сокращения времени прогрева. Во время работы системы Start-stop при заглушенном моторе гидравлика также сохраняет давление масла в гидроаккумуляторе.
Коробка облегчена до 90 кг, что потребовало от инженеров ZF нестандартных решений. Так, в конструкции используются одноразовые алюминиевые болты как для соединения частей коробки друг к другу, так и для крепления гидроблока к корпусу. Само собой они требуют точного усилия при затяжке. Нововведения, связанные с весом, также привели к тому, что КПП теперь официально рекомендовано разбирать в вертикальном положении. Это необходимо для того, чтобы не повредить тонкий алюминиевый лист колбы с планетами. Сам корпус КПП истончен настолько, что инженеры ZF разработали специальную металлическую упор-подкладку, чтобы металл не погнулся от упора обычной стамески.
Эти автоматы чувствительны к качеству масла. Его необходимо менять строго раз в 60-80 тысяч км пробега вместе с фильтром. Если же пренебречь рекомендациями, то металлическая стружка в первую очередь ударит по соленоидам, навлекая проблемы с переключениями передач. По информации концерна ZF, максимальный крутящий момент для коробки составляет приличные 450Н•м, а ресурс без ремонта 250 000 км пробега. Если же постоянно вдавливать до отсечки, то к 150 000 произойдет износ втулок на валах, к которым прикреплены элементы планетарных рядов. На 100 000 км шашечников «порадует» износ фрикционов блокировки, заметный по вибрациям. Поврежденные фрикционы своим шламом потянут за собой соленоиды и гидроблок.
Система полного привода xDrive иногда имеет проблемы с раздатками. Повышенные нагрузки на бездорожье выведут из строя редуктор, который у поставщиков автокомпонентов считается «законченным узлом» и продается лишь в сборе. То есть перебрать его с заменой отдельных элементов на новые не выйдет, они даже не проходят по номерам. Также периодически стоит поглядывать за пыльниками и сальниками приводов.
Кузов «трешки» содержит много алюминиевых навесных частей. Это требует квалифицированных специалистов.
Другая проблема жестянщиков и маляров – это сверхпрочные материалы, скрытые в коробе силовой конструкции. «Некоторые элементы термообработаны таким образом, что при серьезном ремонте их очень сложно перепилить. Раньше на 39-х кузовах при отсверливании крыльев хватало одного сверла на 10-15 клепок. В последней серии на каждую из них уходит по сверлу», – делится Александр Егоров.
Все что касается ходовой части, адаптивной M-подвески и тормозов не досаждает поломками. Александр Егоров объясняет это малым весом и компактностью узлов тройки. Течь или стук рулевой рейки – большая редкость. Рулевые наконечники и тяги меняют в основном из-за закисания, когда невозможно отрегулировать схождение. Из-за тяжелого передка к 100 000 км пробега в передней подвеске могут подвести амортизаторы, которые предпочтительно менять с опорными подшипниками. На этом же пробеге сзади в многорычажке могут заскрипеть плавающие сайлентблоки в верхних поперечных рычагах. Вопросы вызывает и стабилизатор поперечной устойчивости на задней оси: в диаметре он не больше сигареты.
Справедливости ради отметим, что подвеска стала ремонтопригоднее. Если еще несколько лет назад BMW поставляла алюминиевые элементы в сборе и для замены сайлентблока приходилось менять весь H-образный рычаг, то сегодня существуют ремкомплекты. Нельзя заменить лишь задние шаровые опоры, они впаяны в рычаги. Шрусы ходят по 100 000, а тормозные диски спокойно держат по два комплекта колодок.
Хорошая тяга на низах, уверенное движение на средних оборотах и вполне приемлемая динамика в верхнем режиме переворачивают представления о дизеле. Машина «не стреляет» как в случае с бензиновыми ДВС. TwinPower Turbo в паре с восьмиступенчатым автоматом ZF – это настоящий комбайн, непонятный для студента.
Бизнес, построенный на альтернативе
Сеть столичных центров технического обслуживания «Юнит» успешно работает более 16 лет. Основная специализация независимого сервиса – автомобили BMW, Audi, Mercedes, включая Mini Cooper и Smart. Помимо этого, СТО располагает мощностями и квалифицированными специалистами для работы с большинством премиальных брендов.
«Мы имели возможность получить дилерство еще в конце 90-х, тогда это казалось очень заманчивой затеей. Однако именно тогда было принято трезвое решение отказаться от этого направления развития. Дилерство – это служение одному бренду, требующее четкого выполнения плана продаж, обустройства шоу-рума, сервиса, обучения персонала. Такая модель производства крайне неповоротлива. Ее сложно переориентировать с прямых продаж на сервис, чем сегодня с переменчивым успехов занимаются практически все автосалоны. Первые кризисные явления 2008 года показали правильность выбранного пути и подтвердили наши опасения. Работать одновременно с несколькими премиум-брендами под одной крышей – несбыточная фантазия. Успешная бизнес-конструкция должна базироваться на альтернативе, которую мы предлагаем рынку», – рассказал в беседе Александр Егоров, генеральный директор сервисного центра «Юнит».
Действительно, несмотря на известное имя, сервис предлагает свои услуги по вполне либеральным ценам. Сервис работает по большей части в премиум-сегменте, однако обслуживаются здесь практически любые модели массовых брендов. Здесь на ТО не редко можно встретить Rolls-Royce или Bentley, в то время как в соседнем цехе на подъемниках «висят» скромные Polo и Rapid.
По словам Александра, основные клиенты «Юнита» – это владельцы автомобилей старше 2-х лет. «Однако сегодня все кардинально меняется. В 15-м и 16-м годах мы наблюдаем наплыв владельцев новых автомобилей. Это свидетельствует о том, что так называемая «гарантия дилера», на самом деле гарантия автозавода, перестала быть рычагом удержания клиента. Автолюбители понимают, что вероятность того, что в современной машине заклинит коробку или прогорит поршень на первый-второй год эксплуатации, крайне мала. Поэтому есть ли смысл переплачивать?!» – задается вопросом эксперт.
Сервис находится в состоянии постоянного реформирования, но расширяется не только линейка обслуживаемых брендов. Уже несколько лет «Юнит» является официальным дилером таких мировых концернов как ZF и ATE. Это позволяет предоставлять клиентам длительные гарантии на выполненные работы, подкрепленные обязательствами ведущих мировых производителей автокомпонентов.
В сервисе на Волочаевской установлены 13 подъемников Rotary Lift, одни «ножницы» и стенд регулировки сход-развала. На приемке в день работают 4 мастера-приемщика, каждый в паре с мастером цеха. У последнего в подчинении 3 поста и 6 сотрудников. Такой цех за день пропускает минимум 12 автомобилей. По сути это отдельный сервис с собственной логистикой, инструментом и оборудованием.
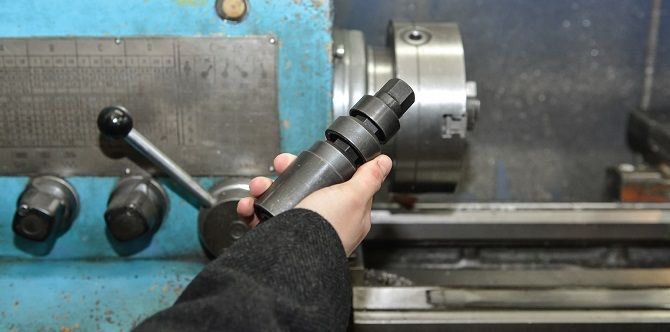
Помимо этого, сервис располагает отделом по диагностике, работающим с оригинальными дилерскими сканерами. Специалисты отдела находятся в постоянном поиске решений нестандартных неисправностей и реализовывают соответствующие программы по обучению коллег. Здесь же работает отдел мотористов и специалистов по ремонту КПП, оборудован кузовной цех с двумя камерами и колорной с системой цветоподбора Glasurit на водной основе. Внимания заслуживает собственный токарный цех. Последний сосредоточен вокруг лучшего станка советских времен – «Красный пролетарий 16К20». Здесь производится собственный специнструмент для обслуживания дизелей, съемники для выпрессовывания плавающих сайлентблоков, штуцеры, фитинги, шпильки и даже целые запасные части. В агрегатном цехе производится переборка моторов и КПП. По сути этих мощностей хватает, чтобы осуществлять срочный ремонт автомобиля любой сложности. Исключение составляют лишь гильзовка и шлифовка блоков, которые производятся на аутсорсе, и промышленное восстановление КПП, которым занимается концерн ZF.
АКПП: вторая жизнь доступна каждому
В 2016 году будут существенно расширены возможности по ремонту и восстановлению агрегатов концерна ZF. И это, безусловно, хорошая новость и для профессионалов СТО, и для конечного клиента. Об этом в специальном интервью для журнала «КУЗОВ» рассказывает Олег Молотков, генеральный директор ООО «ЦФ Руссия», дочерней фирмы концерна «ZF Friedrichshafen AG
– Новые возможности 2016 года по ремонту и восстановлению агрегатов. На чем они базируются?
– В Москве создан центр восстановления и ремонта агрегатов ZF. Напомню: два года назад нами был успешно запущен центр промышленного восстановления агрегатов, входящий в единую глобальную сеть и соответствующий всем самым жестким требованиям. Московский центр был полностью укомплектован персоналом и оборудованием. Он начал работу и вышел на плановые объемы. В центре используются материалы и запчасти проверенного качества, работает обученный в Германии персонал. Налажен сбор агрегатов, сформирован парк обмена и процедура взаимодействия с постоянными партнерами, в первую очередь уровня официальных дилеров брендов – клиентов концерта ZF в оригинальной комплектации. Однако любой бизнес надо постоянно развивать и адаптировать к изменениям на рынке. Учитывая сложную кризисную ситуацию 2015 года и наш опыт работы на рынке в целом, мы приняли решение в 2016 году объединить два проекта: промышленное восстановление агрегатов и ремонт агрегатов. Теперь оба вида работ предлагаются единым фирменным центром.
– Почему было принято такое решение, и возникло два формата работы с агрегатами?
– Причина в том, что мы отчетливо видим две ниши на рынке. Одна из них – именно промышленное восстановление. Эта услуга в первую очередь востребована авторизованными сетями автопроизводителей – BMW, Land Rover и другими марками. Здесь актуальна длительная гарантия на агрегаты, требование по «заливу» наиболее актуальных версий ПО в блоки управления. При промышленном восстановлении используются детали и расходные материалы качества OEM, проводится не только ремонт и замена дефектных узлов и деталей, но и все модернизации, превентивная замена ряда деталей, обновление ПО и так далее. Очевидно, все сказанное довольно внятно определяет и профиль конечного клиента, и уровень гарантий, и ценовую нишу. Агрегат после промышленного восстановления по своим характеристикам аналогичен новому.
Мы исследуем сейчас и вторую нишу, достаточно емкую: это независимый рынок и соответствующая его запросам технология ремонта, а не промышленного восстановления. В чем разница? В первую очередь в экономике. Мы отчетливо увидели в конце 2015 года новое явление для рынка РФ, и довольно массовое: конечный пользователь берет кредит не только для покупки автомобиля, но и для выполнения серьезного ремонта. Отношение к расходам на эксплуатацию, поддержание автомобиля в безопасном и работоспособном состоянии меняется.
Назову и второй фактор для выделения двух разных ниш – это сама специфика организации бизнеса, в том числе его логистики. Для промышленного восстановления требуются так называемые «коры» (CORE) – агрегаты под восстановление. Промышленное восстановление – это по сути производство, и важно сформировать стабильные поставки «сырья». Подобный поток на входе в цех сегодня могут обеспечить только авторизованные сервисные сети, у них широчайшее сбытовое и сервисное покрытие. Сегодня именно дилерские сети организуют сбор агрегатов на центральный склад для стабильной загрузки цеха по восстановлению. И, соответственно, они же получают со склада готовые, восстановленные агрегаты по потребности.
Работа на независимом ремонтном рынке имеет другие «правила». Здесь фактически невозможно наладить стабильные по объемам и регулярности потоки агрегатов под загрузку цеха. Кроме того, клиент нацелен на идею ремонта именно «своей» КПП с последующей установкой на автомобиль, он неоднозначно воспринимает идею получения какой-то чужой, обменной КПП. В этом канале регламент работы иной, чем при промвосстановлении: КПП демонтируется на СТО и поступает в наш фирменный центр ремонта и восстановления, там делается полная дефектовка, определяется экономическая эффективность ремонта и просчитываются ценовые варианты. Лишь после согласования проводится сам ремонт.
Ремонт воспринимается клиентом как привлекательная альтернатива, хотя его цена может составлять +/- 20% от цены обменного агрегата, прошедшего полную процедуру промышленного восстановления. Специалисты нашего центра оценивают рациональность ремонта и состояние агрегата, его ресурс.
Мы передаем данные по ценам, срокам и технологиям в СТО. Конечный клиент получает окончательные и точные данные (с учетом монтажа-демонтажа, транспортировки и т. д.) именно оттуда – от своей СТО он обсуждает с мастером все возможности и принимает решение.
– Как проводится ремонт агрегатов?
– После диагностики принимается решение о допустимости ремонта: у агрегата значительный ресурс, повреждения незначительны, безопасная и надежная работа после ремонта будет обеспечена, цена ремонта укладывается в рамки разумного. В процессе ремонта подлежат замене и детали, вышедшие из строя, и детали, имеющие малый остаточный ресурс. Клиент после выходного контроля качеств получает отремонтированный агрегат с гарантией, а также четкий перечень деталей и узлов, которые были заменены.
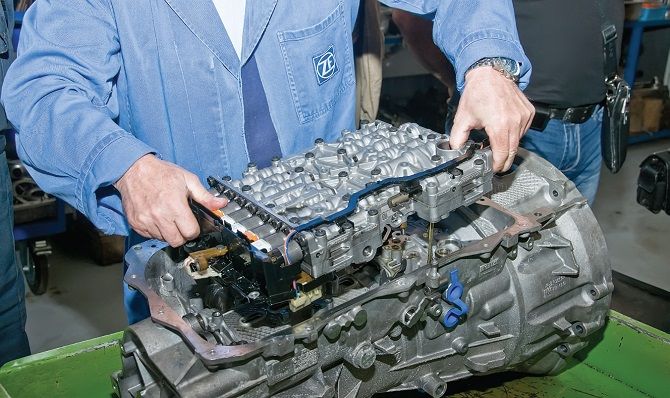
– Частное лицо напрямую не может обратиться в фирменный центр ремонта и восстановления?
– Это наша позиция. Монтаж и демонтаж агрегата, его «прописывание» в системе, подключение – это операции, которые требуют специального оборудования и участия квалифицированного мастера. Учтем и необходимость программирования. Поэтому между центром и клиентом должен быть такой посредник – СТО. Однако к нам может обратиться любая независимая станция технического обслуживания, то есть через свою СТО к нам может попасть по сути любой конечный клиент с запросом на диагностику и ремонт одного агрегата. СТО также может получить доступ к нашему складу готовых агрегатов, восстановленных промышленным методом и имеющих длительную гарантию и фактическое состояние «нового» агрегата.
Комментарии
Рекомендованные статьи
Еще никто не оставил свои комментарии. Ваш комментарий будет первым.