Шиномонтажная эволюция
6 мая 2015, Дмитрий АЛЕКСАНДРОВ
В любой шинной мастерской, будь то цех официального сервисного центра, бокс при специализированном магазине или «шиномонтаж» у дороги, центральным элементом оборудования на протяжении десятилетий были и остаются монтажные и балансировочные станки. В течение долгого времени они оставались примитивными приспособлениями, сваренными из стальных труб, и лишь в 80-е годы постепенно начали превращаться в сложные многофункциональные устройства.

Приблизительно к этому времени относится появление доступных микропроцессоров и последовавший за этим бурный расцвет электроники и автоматики, затронувшей все области производства. В результате шиномонтажные и балансировочные станки перестали быть механическими приспособлениями, позволявшими снять покрышку при помощи монтировки и отбалансировать готовое колесо с невысокой точностью. В процессе эволюции некоторые устройства «обросли» таким количеством новых автоматизированных функций, что превратились, по сути, в роботов, исключающих ручной труд и обходящихся практически без участия оператора.
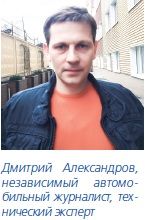
Наивысшим проявлением автоматизации шиномонтажных станков на данный момент стали полностью автоматические шиномонтажные стенды, такие как Hunter Revolution TCR1. Стенд выполняет все необходимые операции в автоматической последовательности, присутствие человека необходимо лишь для запуска операции и визуального контроля работы. Основное преимущество полностью автоматизированного стенда в том, что монтаж и демонтаж колеса любого размера и типа занимает одинаковое и очень небольшое время. В частности, TCR1 демонтирует колесо за 1 минуту и 20 секунд и монтирует его всего за 40 секунд. Квалификация оператора, работающего с полностью автоматическим станком, перестала иметь определяющее значение. Управляя процедурой монтажа и демонтажа одной педалью, он фактически превратился в контролера ОТК. Необходимость в ручных операциях отпала с развитием гидравлических и еще более надежных пневматических приводов.
Необходимо отметить, что полностью автоматические стенды остаются на данный момент наиболее редким видом оборудования за счет высокой стоимости, поэтому наиболее распространенными являются полуавтоматические устройства. Такие станки выполняют самостоятельно отдельные операции, предоставляя человеку возможность только задавать их порядок и в некоторых случаях выполнять действия, требующие высокой точности, например, заводить монтажную головку в пространство между краем борта и ободом.
Развитие электронного управления и применение новых технологий прекрасно прослеживается и на примере балансировочных и диагностических стендов. Эти аппараты снабжены дополнительными устройствами, позволяющими изучать состояние шин и дисков. Наиболее современные стенды работают по технологии бесконтактных лазерных измерений – несколько (до 5) CCD-камер сканируют обод с разных сторон так называемыми 3D лазерными полосами. По результатам прохождения цикла измерений все параметры колеса, в том числе места возможного возникновения дефектов, определяются автоматически и с предельной точностью.
Лазерное сканирование дает возможность получать информацию о целом ряде различных параметров: автоматически определять тип и размер колес; обнаруживать стертые пятна на шине, возможные места повреждения боковины; измерять радиальное и боковое биение шин и обода; определять места установки грузов за спицы; измерять глубину протектора в пяти различных позициях и проецировать терехмерное изображение протектора на экран; а также осуществлять статическую и динамическую балансировку.
Кроме обнаружения дефектов система автоматического обмера диска позволяет совершать своего рода многоходовые комбинации. Иными словами, память устройства сохраняет все данные по колесам, входящим в комплект, чтобы их в дальнейшем можно было сравнить и распределить по позициям на осях автомобиля. Распределение шин в зависимости от степени и характера износа позволяет свести возможность увода автомобиля в сторону от линии движения практически к нулю. В случае с премиальными и спортивными автомобилями, развивающими скорость до 200 и выше километров в час, любое улучшение точности монтажа и балансировки шин имеет прямое и значительное влияние на безопасность.
Помимо повышения точности выполнения операций, развитие электронных компонентов и программного обеспечения привело и к созданию высокоуровневого интерфейса шиномонтажных станков и балансировочных стендов. К примеру, в конструкции балансировочного станка Hofmann geodyna optima II plus предусмотрен цветной 19˝ TFT монитор для визуализации результатов измерений и сенсорный экран, обеспечивающий простое и оперативное управление функциями на уровне смартфона. На данный момент такой интерфейс уже не является новинкой и представляет собой рыночный стандарт для устройств определенного уровня и ценовой категории.
Эволюция любого устройства – комплексный процесс, который складывается из развития отдельных элементов. Развитие электронных технологий привело к скачку в эволюции станков, но этого бы не произошло, если бы к тому моменту они оставались все теми же простыми устройствами из сварных труб с монтажным столом или балансировочной осью.
Если рассматривать процесс развития механики шиномонтажных станков, можно заметить, что катализатором их эволюции не раз становились технологические нововведения в области производства шин и дисков. К примеру, появление легкосплавных дисков с покрытием из хрома и никеля, а затем и с лакокрасочным покрытием, требовало адекватного ответа от производителей шиномонтажного оборудования, так как работа с ними при помощи обычной монтировки приводит к неизбежному возникновению повреждений.
Эволюцию можно проследить на примере конструкции полуавтоматического или автоматического станков, в которых каждый рабочий элемент прошел путь совершенствования для соответствия современным требованиям.
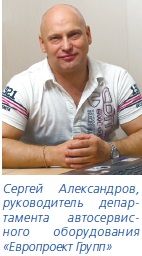
По словам Сергея, круглые столы более универсальны и вошли в обиход с расширением ассортимента дисков и появлением легковых шин большого диаметра. На круглый стол проще уложить тяжелый диск и отцентрировать его. С круглым столом возможна работа любых дополнительных устройств для отжима борта покрышки, поэтому в случае приобретения автоматического или полуавтоматического оборудования с большим количеством дополнительных устройств, стол, вероятнее всего, окажется круглым или производной формы, представляющей нечто среднее между кругом и квадратом. Распространение получили, в частности, шестиугольные или крестообразные столы, чья форма также не создает затруднений для подвода к колесу дополнительных устройств.
Обязательное для стола устройство зажима также прошло путь развития. Современный стол оснащен зажимным устройством, состоящим из раздвижных кулачков с пневматическим приводом. Если раньше встречались устройства, позволяющие захватывать колесо с внешней стороны, то с появлением в конструкции легковых автомобилей дисков диаметром 28 и более дюймов их заменили зажимы, захватывающие обод диска с внутренней стороны. При такой конструкции крепление остается надежным, а размер стола не увеличивается при работе с большими диаметрами.
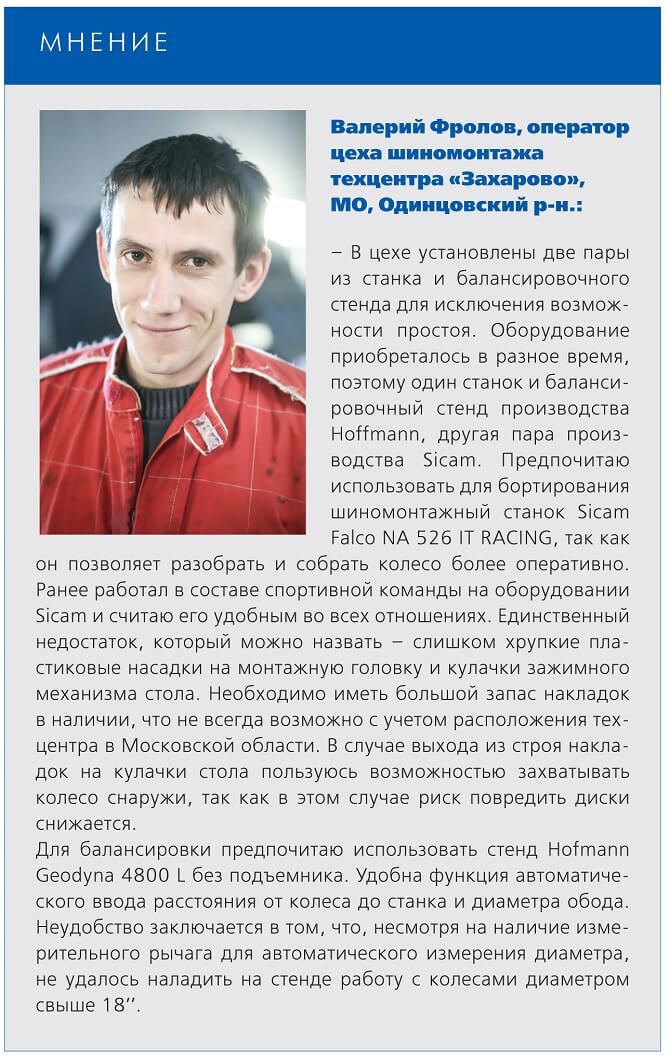
Основной инструмент станка – монтажная лапка, заменившая монтировку, также значительно изменилась в процессе эволюции. Разработчикам удалось постепенно придать монтажной лапке определенную форму и характерный профиль, исключающий нанесение повреждений дорогостоящим шинам и дискам. Некоторые производители для предупреждения повреждений комплектуют лапку специальной пластиковой насадкой.
Еще один пример развития – появление «третьей руки», то есть дополнительной монтажной лапки на отдельной балке, обеспечивающей возможность подводить ее к противоположной стороне обода. Необходимость в ней также возникла в связи с появлением новых технологий в производстве шин – сначала низкопрофильных покрышек, а затем шин типа run-flat.
Обязательным элементом конструкции полуавтоматического монтажного станка стала откидная подводящаяся стойка, служащая своего рода механической «рукой» для крепления монтажной лапки. Стойка, занимающая в рабочем состоянии вертикальное положение, снабжена горизонтальной балкой, которую можно отводить вправо или влево, меняя положение лапки, закрепленной на конце повернутого вниз вертикального штока. Откидная стойка позволяет не только передвигать лапку в горизонтальной плоскости, но и после нахождения нужной позиции опускать ее, чтобы приступить к работе. Такой стойкой оборудованы практически все полуавтоматические станки, и этим они чаще всего отличаются от «автоматов», в которых перемещение лапки может быть устроено по иному принципу.
В ограниченных рамках статьи перечислить все аксессуары, появившиеся в результате развития техники и автоматики невозможно, тем более что многие крупные производители обладают собственными командами разработчиков и предлагают свои уникальные решения для типовых задач, возникающих в процессе монтажа и балансировки колес. Тем не менее на основе того, о чем мы рассказали, можно сделать определенные выводы, которые помогут при организации производства.
Существующее оборудование для монтажа и балансировки можно условно разделить на три типа: простое, полуавтоматическое, автоматическое. В связи с этим естественным образом возникло и три ценовых категории оборудования: бюджетное, средней ценовой категории и оборудование класса «премиум». Необходимо отметить, что тип станка и его ценовая категория далеко не всегда находятся в прямой зависимости. В стоимости оборудования играет важную роль и его происхождение, которое в свою очередь можно также разделить на три основных категории. Первая – европейское оборудование, обладающее преимуществом высокого качества и точности производства. Вторая – бренды из менее развитых европейских стран и крупные китайские производители. Третья – малоизвестные китайские производители, специализирующиеся в основном на производстве самых простых станков.
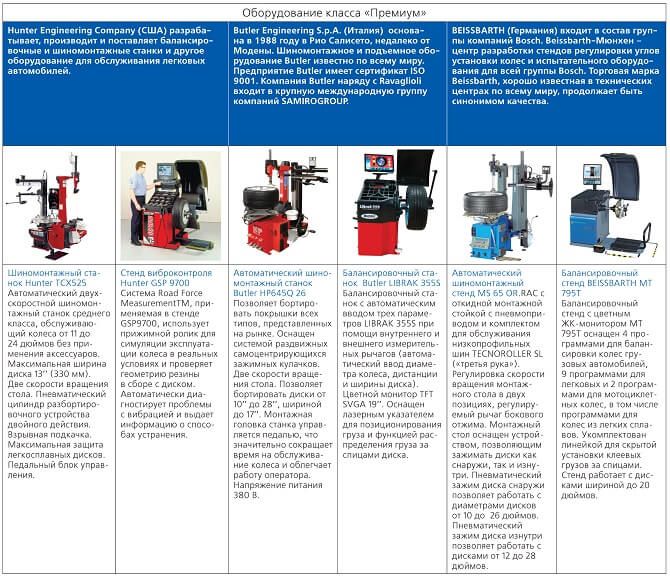
Таким образом, к премиальному классу может относиться полуавтоматический станок, сделанный известной европейской компанией. К премиальному оборудованию, представленному на российском рынке, можно отнести BEISSBARTH, Hunter, Hofmann и тому подобные. К средней ценовой категории относятся станки Giuliano, Vertex, MB Engineering, Bosch и прочее. Бюджетные бренды – Unit, станки российских производителей.
Выбор между типами должен иметь исключительно экономические обоснования. При этом следует помнить, что стоимость оборудования и необходимые инвестиции в его покупку – лишь один из критериев, используемых в экономических расчетах производства.
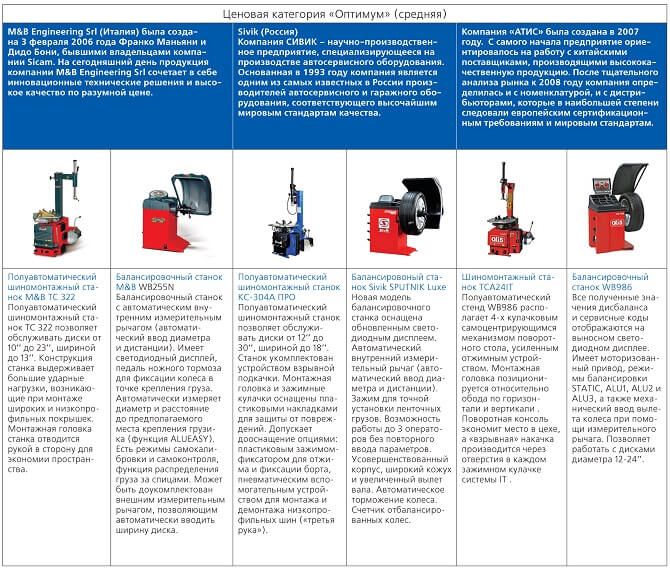
Полуавтоматическое оборудование в первую очередь позволяет экономить такой важный экономический ресурс, как время, так как полный цикл сборки колеса занимает меньше времени, по сравнению с механическим станком, и требует меньших трудозатрат со стороны оператора. По этой причине при низкой загрузке шиномонтажной мастерской вполне можно обойтись примитивным оборудованием. Нередко бывает так, что платить зарплату двум операторам и иметь два простых станка выгодней, чем приобретать дорогой полуавтоматический станок, так как при существующем потоке клиентов срок его окупаемости будет слишком длительным.
Кроме загрузки следует учитывать и типы колес, с которыми придется иметь дело при работе. В настоящий момент можно встретить колеса четырех общих типов: стандартные шины на штампованных дисках, стандартные шины на легкосплавных дисках, низкопрофильные шины на литых дисках, низкопрофильные шины на специальных легкосплавных дисках. Тип колес, с которыми вам приходится работать чаще всего, также влияет на выбор оборудования. Если речь идет, к примеру, о цехе шиномонтажа крупного технического центра, обслуживающего бюджетные модели, полуавтоматический станок просто необходим, а вот от покупки балансировочного стенда с 3D лазерным сканированием, скорее всего, можно воздержаться – стандартные шины на недорогих литых дисках не требуют той точности балансировки, которую обеспечивает это оборудование.
Все эти факторы учитываются на момент создания экономического расчета будущего производства. Однако не нужно быть экономистом, чтобы сделать заключение о том, что дилерскому центру крупного глобального бренда в силу высокого статуса больше подходит оборудование класса «премиум», даже если оно периодически не слишком сильно загружено. Если же говорить о мастерских, чей заработок напрямую зависит от загрузки, скорости и качества обслуживания, то для такого бизнеса лучше всего приобретать полуавтоматическое оборудование средней ценовой категории от известного производителя, для которого доступна целая система аксессуаров и дополнительных приспособлений. Такое оборудование позволит бизнесу сохранять максимальную гибкость в любых обстоятельствах. Как бы ни менялся состав клиентских автомобилей и их количество, чтобы подстроиться под новые условия, достаточно будет докупить дополнительные аксессуары, например «третью руку» под низкопрофильную резину или гидравлический лифт для больших колес. Что же касается небольших мастерских, зарабатывающих в большей степени ремонтом колес, нежели чем их заменой, то для них вполне подойдет простое механическое оборудование, и его происхождение будет зависеть исключительно от доступного объема первоначальных инвестиций.
Комментарии
Рекомендованные статьи
Еще никто не оставил свои комментарии. Ваш комментарий будет первым.