Подшипник вполоборота
27 апреля 2016, Павел СОРОЧИНСКИЙ
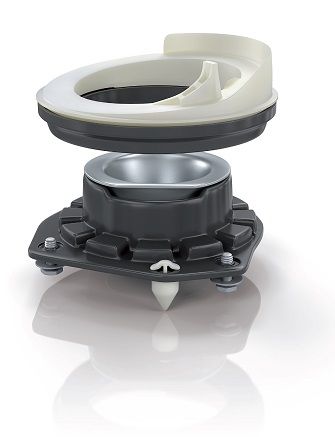
На первый взгляд опорный подшипник амортизационной стойки может показаться деталью не столь сложной в изготовлении – ведь он за свою жизнь не делает такого большого числа оборотов, как другие подшипники. Однако именно эта специфика работы, в сочетании с критической важностью для безопасности движения, накладывает особые требования.
Опорный подшипник – обязательный элемент конструкции, в которой вместе с поворотным кулаком поворачивается сам амортизатор или амортизаторная стойка. Он находится над передней пружиной, через него проходит шток амортизатора. Предназначение опорного подшипника – гашение возникающих в пружине подвески колебаний и напряжений, а также обеспечение мягкого и плавного управления и жесткости радиального направления.
Неисправность подшипника приводит к нарушению углов установки колес, влияет на безопасность вождения и провоцирует быстрый выход из строя стойки амортизатора.
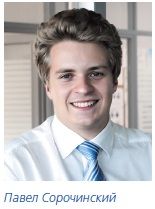
Действительно, опорный подшипник не вращается, а поворачивается вокруг исходного положения, поскольку автомобиль чаще движется по прямой. В среднем 80% времени тела качения находятся в одном месте, а значит, их износ идет неравномерно. Этим и определяются особые требования к смазке и используемым материалам. Основными факторами износа опорного подшипника являются неровности дорожного покрытия и загрязненность, а не естественная выработка ресурса при работе в штатных условиях.
Движение по неровностям ускоряет естественный процесс износа, а при попадании колеса в глубокие ямы, сопровождавшееся «пробоем» подвески, возможна пластическая деформация деталей подшипника с последующим быстрым выходом из строя. Загрязненность же приводит к абразивному износу или блокировке подшипника в опоре с затруднением рулевого управления.
Нормальный ресурс опорного подшипника в стандартных условиях эксплуатации составляет 70-100 тыс. км, что примерно соответствует ресурсу амортизатора. Поэтому при замене амортизатора рекомендуется заменить и опорный подшипник, поскольку оценка его остаточного ресурса при отсутствии видимых повреждений не представляется возможной. Замена тем более актуальна, что его установка при замене амортизационной стойки не требует дополнительного времени. В противном случае, давая гарантию на новый амортизатор, СТО рискует создать рекламационный случай.
Естественно, на практике указанное правило соблюдается не всегда, либо ранее при замене мог быть использован некондиционный подшипник, поэтому при «тугости» рулевого управления следует осматривать опорный подшипник и прилегающие к нему детали. Наиболее простой способ определить состояние опорного подшипника – открыть капот, взяться рукой за стойку амортизатора в месте ее крепления к кузову и резко покачать из стороны в сторону (или попросить кого-то толкать крыло вбок). Если в подшипнике есть люфт или он рассыпался, стойка будет двигаться относительно кузова с характерными щелчками.
Новый опорный подшипник должен свободно вращаться в руках, без «закусываний» и треска. Правда, такая проверка качества является весьма поверхностной. Лучше все-таки довериться продукции производителя с безупречной репутацией. В этом плане настоящим экспертом по опорным подшипникам является корпорация NTN-SNR, лидирующая в разработке и производстве опорных подшипников для стоек передней подвески МакФерсон с суточным объемом выпуска в 90000 штук.
Чтобы понять, что производство высококачественных опорных подшипников не простая задача, стоит рассмотреть, как новый тип подшипника испытывается в лаборатории NTN-SNR на соответствие техническим спецификациям автопроизводителей. Комплекс предсерийных испытаний длится от одного до трех лет. Определяется жизненный цикл изделия (наработка на отказ) в приближенных к реальным условиям (воздействие грязи, соли, воды). При этом должны сохраняться в целостности уплотнения, обеспечивающие устойчивость к коррозии.
Должен быть строго соблюден момент сил трения, а изменение момента сопротивления вращению на протяжении всего жизненного цикла должно составлять не более 30%. Также на стенде при различных нагрузках проводятся испытания на устойчивость к бринеллированию (возникновению точечных углублений на дорожках качения). Стенд для проведения ресурсных испытаний симулирует работу передней подвески по алгоритмам, моделирующим различные типы дорог и стили вождения.
При конструировании подшипников NTN-SNR использует ПО собственной разработки для моделирования процессов. Подшипники NTN-SNR оснащаются все большим количеством новых функций (седло пружины, упор буфера хода сжатия), в них применяются инновационные подходы: полимерные материалы для снижения веса узла, оригинальные решения по защите от загрязнений и т.д. Основная гамма продукции производится во Франции, также у компании есть производство в Японии и Германии. Производственная гамма покрывает 84% автопарка мира.
Качество подшипников создало фирме репутацию, и потому некоторые производители прибегают к имитации формы и цвета деталей NTN-SNR, чтобы создать впечатление сопоставимости ее по качеству с оригинальной. Однако плохое качество стали, смазки и пластика, неадекватная термическая обработка (закалка) или ее отсутствие – все это может оказать серьезное негативное влияние на срок службы деталей. Использование подобной продукции может привести к повреждению других компонентов подвески и деталей кузова автомобиля.
Помимо низкого качества самого подшипника одной из причин отказов может стать некорректная сборка при замене. Крайне важно использовать при замене все компоненты из набора: винты, болты, гайки и другие компоненты. NTN-SNR включает в свои наборы все компоненты верхней части подвески: подшипники, винты, болты, изолирующие/амортизирующие детали. Каждый компонент испытывается и проверяется сотрудниками отдела контроля качества (тестирование жизненного цикла, анализ твердости материала, анализ химического состава стали). За последние 10 лет NTN-SNR не выпущено в продажу ни одной бракованной детали, что обеспечивается селективной сборкой* и 100% тестированием всей выпускаемой продукции.
*Селективная сборка – метод сборки узлов, при котором подбираются сопряженные детали. Поступающие на сборку компоненты сортируются по размерным группам, внутри которых сопрягаемые детали имеют наиболее благоприятные для соединения фактические размеры (с наиболее близкими полями допусков). При изготовлении прецизионных изделий селективная сборка позволяет в разы повысить точность сборки там, где уменьшение допусков уже невозможно технически.
Если вы интересуетесь темой удаления царапин, прочитайте нашу статью "Как удалить царапины на бампере автомобиля своими руками".
Комментарии
Рекомендованные статьи
Еще никто не оставил свои комментарии. Ваш комментарий будет первым.